Preparation method for polymer-containing crude oil demulsifier
A crude oil demulsifier and polymer technology, which is applied in the field of preparation of polymer-containing crude oil demulsifier, can solve the problems of inability to effectively treat polymer-containing crude oil, poor water quality of the extracted sewage, etc., and achieve good performance of polymer-containing emulsified crude oil. , Good hydrophilic and lipophilic properties, strong surface activity effect
- Summary
- Abstract
- Description
- Claims
- Application Information
AI Technical Summary
Problems solved by technology
Method used
Examples
preparation example Construction
[0019] (1) Preparation of intermediates: Add 0.5 parts by weight of catalyst sodium ethoxide and 1.5 parts by weight of initiator polyethylene glycol into a stainless steel autoclave, vacuumize and fill with nitrogen three times at 20-30°C To replace the air in the kettle, raise the temperature to 120°C, feed 98 parts by weight of propylene oxide, and control the reaction pressure to 0.2-0.4MPa, and reduce the pressure after 2 hours until the pressure does not change anymore, to obtain the intermediate;
[0020] (2) Preparation of ethylene oxide and propylene oxide block copolyether: Add 0.3 parts by weight of catalyst sodium ethoxide and 20 parts by weight of the intermediate prepared in step (1) into a stainless steel autoclave, and vacuumize and nitrogen gas three times respectively, feed 79.7 parts by weight of ethylene oxide, control the reaction temperature to 120°C, and the reaction pressure to 0.2-0.4MPa, reduce the pressure after 2 hours until the pressure no longer ch...
Embodiment 1
[0026] The present invention is realized through the following steps:
[0027] (1) Preparation of intermediates: Add 0.5 parts by weight of catalyst sodium ethoxide and 1.5 parts by weight of initiator polyethylene glycol into a stainless steel autoclave, vacuumize and fill with nitrogen three times at 20°C to replace The air in the kettle is heated up to 120°C, 98 parts by weight of propylene oxide is introduced, and the reaction pressure is controlled to be 0.2MPa, and the pressure is reduced after 2 hours until the pressure does not change anymore, and the intermediate is obtained;
[0028] (2) Preparation of ethylene oxide and propylene oxide block copolyether: Add 0.3 parts by weight of catalyst sodium ethoxide and 20 parts by weight of the intermediate prepared in step (1) into a stainless steel autoclave, and vacuumize and nitrogen gas three times each, feed 79.7 parts by weight of ethylene oxide, control the reaction temperature to 120°C, and the reaction pressure to 0...
Embodiment 2
[0033] The present invention is realized through the following steps:
[0034] (1) Preparation of intermediates: Add 0.5 parts by weight of catalyst sodium ethoxide and 1.5 parts by weight of initiator polyethylene glycol into a stainless steel autoclave, vacuumize and fill with nitrogen three times at 25°C to replace The air in the kettle was heated up to 120°C, 98 parts by weight of propylene oxide was introduced, and the reaction pressure was controlled to be 0.3MPa, and after 2 hours, the pressure was reduced until the pressure did not change to obtain the intermediate;
[0035] (2) Preparation of ethylene oxide and propylene oxide block copolyether: Add 0.3 parts by weight of catalyst sodium ethoxide and 20 parts by weight of the intermediate prepared in step (1) into a stainless steel autoclave, and vacuumize and nitrogen gas three times respectively, feed 79.7 parts by weight of ethylene oxide, control the reaction temperature to 120°C, and the reaction pressure to 0.3M...
PUM
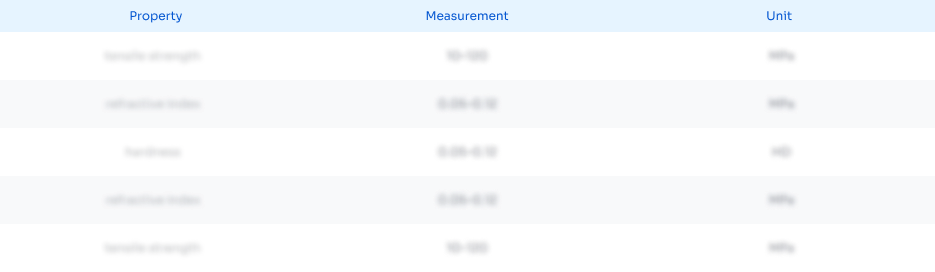
Abstract
Description
Claims
Application Information

- R&D Engineer
- R&D Manager
- IP Professional
- Industry Leading Data Capabilities
- Powerful AI technology
- Patent DNA Extraction
Browse by: Latest US Patents, China's latest patents, Technical Efficacy Thesaurus, Application Domain, Technology Topic, Popular Technical Reports.
© 2024 PatSnap. All rights reserved.Legal|Privacy policy|Modern Slavery Act Transparency Statement|Sitemap|About US| Contact US: help@patsnap.com