Gold tailing treatment process
A treatment process, technology for gold mine tailings, applied in the direction of solid separation, wet separation, chemical instruments and methods, etc., can solve the problems of low production technology level, low recovery rate, poor production indicators, etc.
- Summary
- Abstract
- Description
- Claims
- Application Information
AI Technical Summary
Problems solved by technology
Method used
Image
Examples
Embodiment Construction
[0013] see figure 1 Shown, the gold ore tailings treatment process of the present invention comprises the following process steps:
[0014] (1) First, the original tailings slurry is re-selected and separated through the spiral chute 1. The width of the selection area of the spiral chute 1 is set to 8-9CM. The width can be adjusted according to the site. The spiral chute recycles the large-grained ore pulp within the width of 8-9CM. Use the fine-grained slurry outside the width of 8-9CM for tailings filling;
[0015] (2) the ore pulp recovered in step (1) is carried out through the first single-layer thickener 2 to separate water and ore, and the separated water is discharged;
[0016] (3) the ore that step (2) is obtained is ground by ball mill 3, and the ore fineness of grinding is that the ore particles passing through the 200 hole / square inch sieve have 55 ± 2%, and the pulp concentration is 33 ± 2%;
[0017] (4) The ore processed in step (3) is sent to classifier 4 fo...
PUM
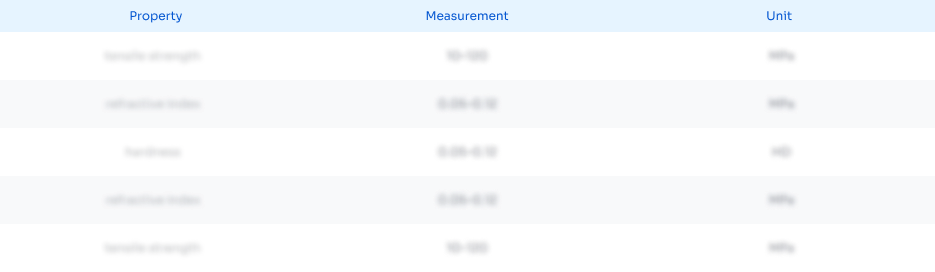
Abstract
Description
Claims
Application Information

- R&D Engineer
- R&D Manager
- IP Professional
- Industry Leading Data Capabilities
- Powerful AI technology
- Patent DNA Extraction
Browse by: Latest US Patents, China's latest patents, Technical Efficacy Thesaurus, Application Domain, Technology Topic, Popular Technical Reports.
© 2024 PatSnap. All rights reserved.Legal|Privacy policy|Modern Slavery Act Transparency Statement|Sitemap|About US| Contact US: help@patsnap.com