Method for preparing bamboo pulp with full liquid phase pre-hydrolytic sulfate rapid displacement cooking
A technology of displacement cooking and pre-hydrolysis, which is applied in pulping with inorganic alkali, pulp bleaching, post-treatment of cellulose pulp, etc., can solve the problems of bamboo pulp production capacity limitation, unstable hydrolysis, long heating time, etc., to save heating Time and steam, solve the effect of large waste water pollution and reduce waste water pollution
- Summary
- Abstract
- Description
- Claims
- Application Information
AI Technical Summary
Problems solved by technology
Method used
Examples
Embodiment 1
[0021] Material preparation: Bamboo is cut into 20-50mm long rectangular bamboo slices by a bamboo cutting machine, and the pass rate is required to reach more than 80%.
[0022] Washing: The bamboo slices are washed by a washing machine to remove surface impurities and excess water, and then enter the cooking pot.
[0023] Pre-hydrolysis: After washing, the bamboo chips are packed in a pot according to the packing density of 200kg / m3, and then the hydrolysis medium is filled into the cooking pot. Keep at 165°C for 180 minutes. After the hydrolysis is completed, the hydrolyzate is pumped into the hydrolyzate storage tank as the next pot of hydrolysis medium.
[0024] Cooking: using sulfate full liquid phase cooking. The amount of alkali used is Na 2 O is 22% to the absolute dry bamboo weight, and the degree of sulfidation is based on Na 2 O is 25%, rising to 160°C for 120 minutes, discharging after completion of terminal replacement, yielding a slurry yield of 34%, a cellul...
Embodiment 2
[0031] Material preparation: Bamboo is cut into 20-50mm long rectangular bamboo slices by a bamboo cutting machine, and the pass rate is required to reach more than 80%.
[0032] Washing: The bamboo slices are washed by a washing machine to remove surface impurities and excess water, and then enter the cooking pot.
[0033] Pre-hydrolysis: after washing, the bamboo chips are packed in a pot according to the packing density of 200kg / m3, and then the cooking pot is filled with hydrolysis medium and then the temperature is raised. Keep at ℃ for 180 minutes. After the hydrolysis is completed, the hydrolyzate is pumped into the hydrolyzate storage tank as the next pot of hydrolysis medium.
[0034] Cooking: using sulfate full liquid phase cooking. The amount of alkali used is Na 2 O is 22% to the absolute dry bamboo weight, and the degree of sulfidation is based on Na 2 O is 25%, rising to 165°C for 140 minutes, discharging after completion of terminal replacement, yielding a sl...
Embodiment 3
[0041] Material preparation: Bamboo is cut into 20-50mm long rectangular bamboo slices by a bamboo cutting machine, and the pass rate is required to reach more than 80%.
[0042] Washing: The bamboo slices are washed by a washing machine to remove surface impurities and excess water, and then enter the cooking pot.
[0043]Pre-hydrolysis: After washing, the bamboo chips are packed in a pot according to the packing density of 200kg / m3, and then the cooking pot is filled with hydrolysis medium and then the temperature is raised. The temperature is kept at 120 minutes. After the hydrolysis is completed, the hydrolyzate is pumped into the hydrolyzate storage tank as the next pot of hydrolysis medium.
[0044] Cooking: using sulfate full liquid phase cooking. The amount of alkali used is Na 2 O is 20% of the absolute dry bamboo weight, and the degree of sulfidation is based on Na 2 O is 20%, rise to 170°C and hold for 120 minutes, discharge after completion of end-point replacem...
PUM
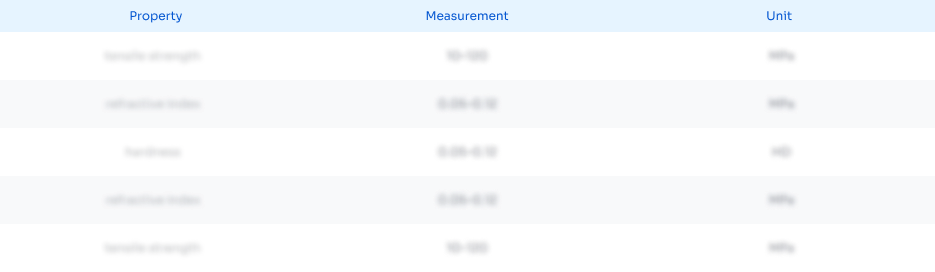
Abstract
Description
Claims
Application Information

- R&D
- Intellectual Property
- Life Sciences
- Materials
- Tech Scout
- Unparalleled Data Quality
- Higher Quality Content
- 60% Fewer Hallucinations
Browse by: Latest US Patents, China's latest patents, Technical Efficacy Thesaurus, Application Domain, Technology Topic, Popular Technical Reports.
© 2025 PatSnap. All rights reserved.Legal|Privacy policy|Modern Slavery Act Transparency Statement|Sitemap|About US| Contact US: help@patsnap.com