Magnesium sulfate heptahydrate production method utilizing waste sulfuric acid from production of cation exchange resin
A technology of cation exchange and waste sulfuric acid, applied in magnesium sulfate and other directions, can solve the problems of black color such as ink, increase the production cost of enterprises, difficult to find users, etc., to solve the problem of waste sulfuric acid treatment, no secondary pollution, and increase efficiency. Effect
- Summary
- Abstract
- Description
- Claims
- Application Information
AI Technical Summary
Problems solved by technology
Method used
Examples
Embodiment
[0008] Embodiment: get concentration and be 50% waste sulfuric acid 1400kg to reaction tank, add 350kg magnesia and carry out mixed reaction, reaction time is 80 minutes, and after reaction, pH value is 6.5, and Baume concentration is 41.
[0009] Then add 5 kg of flocculant (polyacrylamide), stir, wait for the tiny carbides to flocculate into agglomerates and sink, then take the clear liquid to the crystallization tank, adjust the acid, make the whole solution crystallize under the condition of pH value 4, and then Send the crystallized magnesium sulfate heptahydrate into a centrifugal dehydrator to complete.
[0010] The applicant found in the initial exploration that the waste sulfuric acid produced in the production of cation exchange resins is very different from the waste sulfuric acid produced in other productions: except for carbides, it does not contain other metal ions and substances, which is very important. It is the premise that it can be used for magnesium sulfat...
PUM
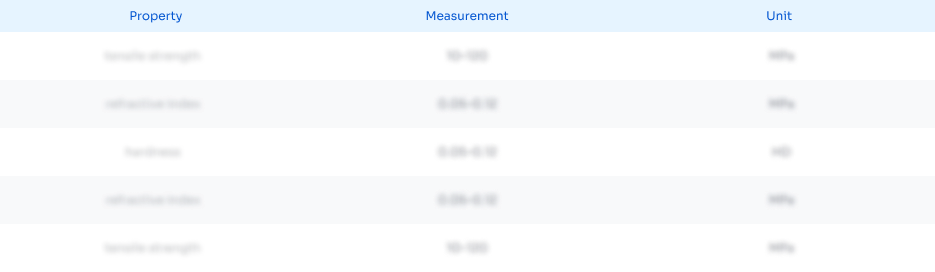
Abstract
Description
Claims
Application Information

- R&D
- Intellectual Property
- Life Sciences
- Materials
- Tech Scout
- Unparalleled Data Quality
- Higher Quality Content
- 60% Fewer Hallucinations
Browse by: Latest US Patents, China's latest patents, Technical Efficacy Thesaurus, Application Domain, Technology Topic, Popular Technical Reports.
© 2025 PatSnap. All rights reserved.Legal|Privacy policy|Modern Slavery Act Transparency Statement|Sitemap|About US| Contact US: help@patsnap.com