Method for extracting uranium from uranium-contained niobium-tantalum leached tailings
A leaching, niobium and tantalum technology, applied in the field of uranium extraction, can solve problems such as radioactive pollution, uranium extraction difficulty, emulsified anion exchange resin poisoning, etc., and achieve the effect of reducing energy consumption, reducing raw material consumption, and high recovery rate
- Summary
- Abstract
- Description
- Claims
- Application Information
AI Technical Summary
Problems solved by technology
Method used
Examples
Embodiment 1
[0019] Step 1, sulfuric acid leaching, weighing 500g of the above-mentioned niobium-tantalum tailings sample into a 2000mL glass beaker, adding 500mL of deionized water, stirring once every 30min, stirring intermittently to leach the free uranium in the tailings, filtering after continuous leaching for 2h, to obtain Uranium-containing leaching solution and solid slag; add 500mL deionized water and 10mL concentrated sulfuric acid to the solid slag, stir once every 30min, continuously leaching for 3h, and filter to obtain uranium-containing leaching solution and solid slag; repeat the previous step 8 times and measure the solid The content of uranium in the slag is less than 82ug / g, and the content of uranium in the 8th sulfuric acid leaching solution is less than 100ug / mL. At this time, the leaching rate of uranium is greater than 90%. The uranium-containing clear liquid is combined for the extraction of uranium in the next step; the leaching solution with a concentration lower ...
Embodiment 2
[0026] The operating condition of embodiment 2 and step are with embodiment 1, and its difference is:
[0027] (1) The deionized water in step one is 1000mL, and the concentrated sulfuric acid is 90mL; after 4 times of leaching, the content of uranium in the solid slag is less than 82ug / g, and the leaching rate of uranium is greater than 90%.
[0028] (2) add 60mL extractant and extract in step 2, extractant consists of 3% two (2-ethylhexyl) phosphonic acid, 3% nonanol and 94% sulfonated solvent kerosene, extraction compared to (O / W): 1 / 5, shake the separatory funnel vigorously for 10 minutes, place it for clarification for 10 minutes, and measure U<0.005g / L in the inorganic phase after 5-stage extraction operation.
[0029] (3) Use 2% H in step three 2 SO 4 Solution 100mL washes twice; Back extraction with 5% ammonium carbonate again, back extraction ratio (O / W) is 2 / 1; Vigorously shake separatory funnel 20min during back extraction, place clarification 30min, back extractio...
Embodiment 3
[0033] The operating condition of embodiment 3 and step are with embodiment 1, and its difference is:
[0034] (1) The deionized water added in step one is 1000mL, and the concentrated sulfuric acid is 50mL; through 6 times of leaching, the content of uranium in the solid slag is less than 82ug / g, and the leaching rate of uranium is greater than 90%.
[0035] (2) Add 40mL to step 2 for extraction, the extractant consists of 8% bis(2-ethylhexyl)phosphonic acid, 2% nonanol and 90% sulfonated solvent kerosene, place it for clarification for 50min, after 6-stage extraction operation It is measured that U<0.005g / L in the inorganic phase.
[0036] (3) Use 2% H in step three 2 SO 4 Solution 100mL washes twice; Back extraction with 15% ammonium carbonate again, back extraction ratio (O / W) is 8 / 1; Vigorously shake separatory funnel 15min during back extraction, place clarification 90min; Back extraction series is Grade 5, the extraction recovery rate is greater than 95%.
[0037] (...
PUM
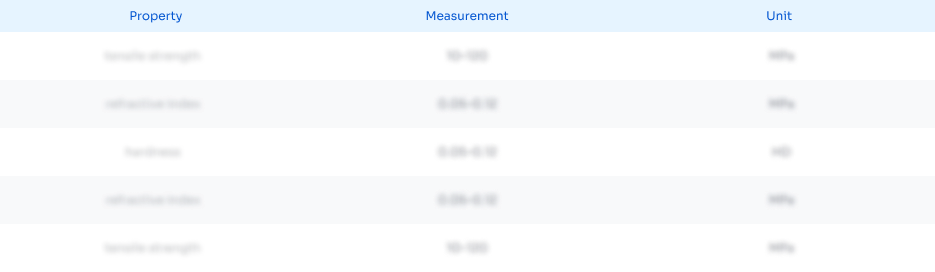
Abstract
Description
Claims
Application Information

- Generate Ideas
- Intellectual Property
- Life Sciences
- Materials
- Tech Scout
- Unparalleled Data Quality
- Higher Quality Content
- 60% Fewer Hallucinations
Browse by: Latest US Patents, China's latest patents, Technical Efficacy Thesaurus, Application Domain, Technology Topic, Popular Technical Reports.
© 2025 PatSnap. All rights reserved.Legal|Privacy policy|Modern Slavery Act Transparency Statement|Sitemap|About US| Contact US: help@patsnap.com