A kind of iron-copper base powder alloy brake pad and preparation method thereof
A powder alloy and brake pad technology, which is applied in the field of iron-copper-based powder alloy brake materials and its preparation, can solve the problems of short service life, high cost of raw materials, low thermal conductivity, etc.
- Summary
- Abstract
- Description
- Claims
- Application Information
AI Technical Summary
Problems solved by technology
Method used
Examples
Embodiment 1
[0018] The present embodiment is a kind of iron-copper base powder alloy brake pad, and the composition of described iron-copper base powder alloy brake pad is as shown in table 1:
[0019] Table 1 Weight ratio of iron-copper-based brake materials
[0020] component iron powder copper powder tin powder Molybdenum powder lead powder Silicon carbide Molybdenum disulfide graphite Granularity (mesh) -200 -200 300 300 -200 100 powder Scaly 80 Weight content (%) 38 38 3 2 5 4 1 9
[0021] The total amount of the components of the iron-copper-based powder alloy brake pad does not exceed 100%.
[0022] This embodiment also proposes a method for preparing an iron-copper-based powder alloy brake pad, and its specific process includes the following steps:
[0023] The first step is raw material pretreatment. The silicon carbide, molybdenum disulfide and graphite flakes were placed in an oven and dried ...
Embodiment 2
[0032] This embodiment is an iron-copper-based powder alloy brake pad, and the components of the iron-copper-based powder alloy brake pad are shown in Table 2:
[0033] Table 2 Weight ratio of iron-copper-based brake materials
[0034] component iron powder copper powder tin powder Molybdenum powder lead powder Silicon carbide Molybdenum disulfide graphite Granularity (mesh) -200 -200 300 300 -200 100 powder Scaly 80 Weight content (%) 30 44 6 1 3 3 2 11
[0035] The total amount of the components of the iron-copper-based powder alloy brake pad does not exceed 100%.
[0036] This embodiment also proposes a method for preparing an iron-copper-based powder alloy brake pad, and its specific process includes the following steps:
[0037] The first step is raw material pretreatment. The silicon carbide, molybdenum disulfide and graphite flakes were placed in an oven and dried at 120°C for 1 hour....
Embodiment 3
[0046] This embodiment is an iron-copper-based powder alloy brake pad. The components of the iron-copper-based powder alloy brake pad are shown in Table 3:
[0047] Table 3 Weight ratio of iron-copper-based brake materials
[0048] component iron powder copper powder tin powder Molybdenum powder lead powder Silicon carbide aluminum disulfide graphite Granularity (mesh) -200 -200 300 300 -200 100 powder Scaly 80 Weight content (%) 45 30 5 1.5 4 3.5 3 8
[0049] The total amount of the components of the iron-copper-based powder alloy brake pad does not exceed 100%.
[0050] This embodiment also proposes a method for preparing an iron-copper-based powder alloy brake pad, and its specific process includes the following steps:
[0051] The first step is raw material pretreatment. The silicon carbide, molybdenum disulfide and graphite flakes were placed in an oven and dried at 120°C for 1 hour. ...
PUM
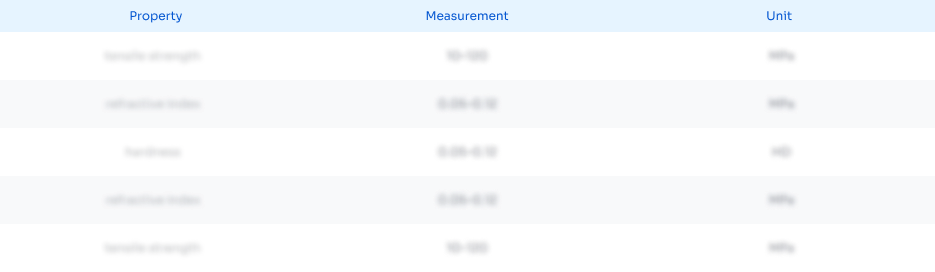
Abstract
Description
Claims
Application Information

- Generate Ideas
- Intellectual Property
- Life Sciences
- Materials
- Tech Scout
- Unparalleled Data Quality
- Higher Quality Content
- 60% Fewer Hallucinations
Browse by: Latest US Patents, China's latest patents, Technical Efficacy Thesaurus, Application Domain, Technology Topic, Popular Technical Reports.
© 2025 PatSnap. All rights reserved.Legal|Privacy policy|Modern Slavery Act Transparency Statement|Sitemap|About US| Contact US: help@patsnap.com