Water-assisted molding process and constant pressure water-assisted injection molding equipment
An injection molding, water-assisted technology, applied in the field of injection molding technology and equipment, can solve the problems of injection water pressure loss impact, long system response time, and rapid melt cooling, etc., to solve the pressure loss impact, which is beneficial to cooling, The effect of high specific heat capacity
- Summary
- Abstract
- Description
- Claims
- Application Information
AI Technical Summary
Problems solved by technology
Method used
Image
Examples
Embodiment Construction
[0036] The present invention will be described in further detail below in conjunction with the accompanying drawings and embodiments. exist Figure 1-12 Among them, each serial number indicates: 1. High-pressure water source, 2. High-pressure nitrogen source, 3. Compressed air source, 4. High-pressure water stop valve, 5. High-pressure nitrogen stop valve, 6. Compressed air stop valve, 7. High-pressure water filter , 8. High pressure nitrogen filter, 9. Compressed air filter, 10. Water injection accumulator, 11. Water injection high pressure solenoid valve, 12. Flow regulating solenoid valve, 13. Gas injection high pressure solenoid valve, 14. Gas injection solenoid valve , 15. High-pressure electric gas valve, 16. First one-way valve, 17. High-pressure electric water valve, 18. Pressure sensor, 19. Program controller, 20. Step-down solenoid valve, 21. Filter, 22. Water tank, 23. Injection molding machine controller, 23-A. Injection mechanism of injection molding machine, 24....
PUM
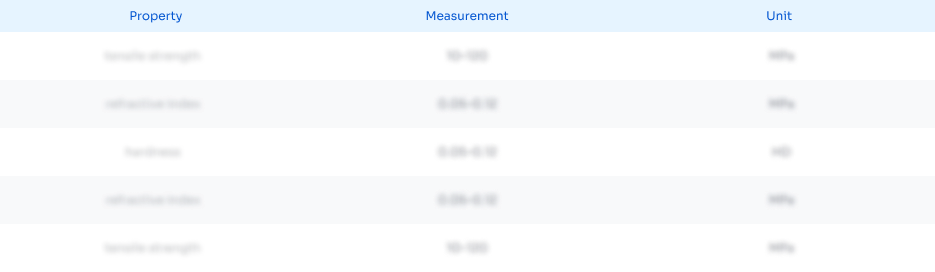
Abstract
Description
Claims
Application Information

- R&D Engineer
- R&D Manager
- IP Professional
- Industry Leading Data Capabilities
- Powerful AI technology
- Patent DNA Extraction
Browse by: Latest US Patents, China's latest patents, Technical Efficacy Thesaurus, Application Domain, Technology Topic, Popular Technical Reports.
© 2024 PatSnap. All rights reserved.Legal|Privacy policy|Modern Slavery Act Transparency Statement|Sitemap|About US| Contact US: help@patsnap.com