Method for surface treatment by developing machine after electronic circuit board anti-soldering process
An electronic circuit board, surface treatment technology, applied in the direction of secondary treatment of printed circuits, etc., can solve the problems of increasing the overflow of composite washing, SMONPAD, increasing the amount of pure water, etc., to improve the yield of PCB production, reduce SMONPAD, The effect of increasing the speed of the developing machine
- Summary
- Abstract
- Description
- Claims
- Application Information
AI Technical Summary
Problems solved by technology
Method used
Examples
Embodiment 1
[0066] The invention discloses a method for surface treatment of an electronic circuit board using a developing machine after the anti-soldering process, using the following process steps:
[0067] 1. Preparation of sodium carbonate solution: prepare sodium carbonate solution by Na2CO3 and tap water; wherein: Na2CO3 19kg, tap water 1900L, add Na2CO3 19kg and tap water 1900L into a bath and stir for 30 minutes, Na2CO3 is completely dissolved and ready to use; the sodium carbonate The purity of Na2CO3 in the solution is: 99.2%.
[0068] 2. One-tank development process
[0069] The PCB board is horizontally driven into the developing machine through the rollers, and the sodium carbonate solution arranged in the first developing tank is pumped out to spray the sodium carbonate solution onto the PCB surface through the nozzle on the spray plate, and the PCB is sprayed under the pressure of the sodium carbonate spray. The unexposed copper side of the board and the ink in the holes ...
Embodiment 2
[0096] The method of the present invention uses a developing machine for surface treatment of an electronic circuit board after the anti-soldering process, including the following process parameters: the purpose of the present invention can also be achieved by using the equipment and process steps in Embodiment 1.
[0097] 1. Prepare sodium carbonate solution: prepare sodium carbonate solution by Na2CO3 and tap water; wherein: Na2CO3 15.2kg, tap water 1900L, add Na2CO3 19kg and tap water 1900L into a bath and stir for 30 minutes, Na2CO3 dissolves completely and is ready to use; The purity of Na2CO3 in sodium solution is: 99.2%.
[0098] 2. One-tank development process
[0099] The height of the nozzle from the PCB board is 13CM. The weight percent concentration of sodium carbonate in the sodium carbonate solution is: 0.8%, and the developing time of the sodium carbonate solution is: 25S / piece. The temperature of the sodium carbonate solution is: 28°C, and the spraying pressu...
Embodiment 3
[0125] A method of using a developing machine for surface treatment of an electronic circuit board according to the present invention includes the following process parameters: the purpose of the present invention can also be achieved by using the equipment and process steps in Embodiment 1.
[0126] 1. Prepare sodium carbonate solution: prepare sodium carbonate solution by Na2CO3 and tap water; wherein: Na2CO3 20.9kg, tap water 1900L, add Na2CO3 19kg and tap water 1900L into a bath and stir for 30 minutes, Na2CO3 dissolves completely and is ready for use; The purity of Na2CO3 in sodium solution is: 99.2%.
[0127] 2. One-tank development process
[0128] The height of the nozzle from the PCB board is 13CM. The weight percent concentration of sodium carbonate in the sodium carbonate solution is: 1.2%, and the developing time of the sodium carbonate solution is: 30S tablets. The temperature of the sodium carbonate solution is: 32°C, and the spraying pressure of the developing...
PUM
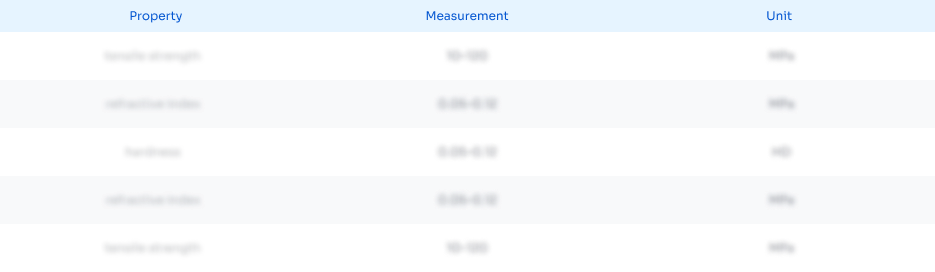
Abstract
Description
Claims
Application Information

- Generate Ideas
- Intellectual Property
- Life Sciences
- Materials
- Tech Scout
- Unparalleled Data Quality
- Higher Quality Content
- 60% Fewer Hallucinations
Browse by: Latest US Patents, China's latest patents, Technical Efficacy Thesaurus, Application Domain, Technology Topic, Popular Technical Reports.
© 2025 PatSnap. All rights reserved.Legal|Privacy policy|Modern Slavery Act Transparency Statement|Sitemap|About US| Contact US: help@patsnap.com