A method for comprehensive utilization of vanadium-titanium magnetite
A technology for vanadium-titanium-magnetite and magnetic separation separation, which is applied in chemical instruments and methods, magnetic separation, and process efficiency improvement, etc. It can solve the problems of serious agglomeration reduction and pulverization, and achieve the effects of being beneficial to environmental protection, short reaction time and shortened production cycle.
- Summary
- Abstract
- Description
- Claims
- Application Information
AI Technical Summary
Problems solved by technology
Method used
Image
Examples
Embodiment 1
[0024] What this embodiment adopts is the vanadium-titanium magnetite in Panzhihua area (composition is TFe54.54%, FeO23.16%, SiO 2 2.934%, CaO0.398%, Al 2 o 3 3.54%, MgO3.7%, S0.292%, TiO 2 10.77%, V 2 o 5 0.666%), and add 20% reducing agent (the composition is fixed carbon 86.47%, volatile matter 8.58%, ash 4.95%, S0.31%), flux (CaF 2 2%) and binder (cornmeal 2.5%), mix well, add water, press into a block, dry at 200-300°C, add to the rotary hearth furnace for high temperature reduction, the temperature in the rotary hearth furnace Keep it at 1350-1500°C, and control the reduction time at 15-45 minutes. After the reduction, magnetic separation separates to obtain high-titanium slag and pearl iron. After the high-titanium slag extracts vanadium, the grade of titanium slag is above 48.73%, and the slag is oxidized The content of ferrous iron is less than 2%, which meets the raw material requirements of sulfuric acid titanium dioxide production process; the iron content of...
Embodiment 2
[0026] What this embodiment adopts is the vanadium-titanium magnetite in Panzhihua area (composition is TFe53.54%, FeO28.16%, SiO 2 2.2%, CaO0.338%, Al 2 o 3 2.74%, MgO1.4%, S0.302%, TiO 2 10.82%, V 2 o 5 0.5%), and add 15% reducing agent (the composition is fixed carbon 86.47%, volatile matter 8.58%, ash 4.95%, S0.31%), flux (Na 2 SO 4 3%, CaF 2 2%) and binder (cornmeal 1.5%), mix well, add water, press into a block, dry at 200-300°C, add to the rotary hearth furnace for high temperature reduction, the temperature in the rotary hearth furnace Keep it at 1350-1500°C, and the reduction time is controlled at 15-45min. After the reduction, magnetic separation separates to obtain high-titanium slag and pearl iron. After the high-titanium slag extracts vanadium, the grade of titanium slag is above 49.64%, and the slag is oxidized The content of ferrous iron is less than 2%, which meets the raw material requirements of the sulfuric acid titanium dioxide production process; th...
Embodiment 3
[0028] What this embodiment adopts is the vanadium-titanium magnetite in Panzhihua area (composition is TFe55.34%, FeO29.07%, SiO 2 2.3%, CaO0.32%, Al 2 o 3 2.45%, MgO1.21%, S0.35%, TiO 2 8.27%, V 2 o 5 0.69%), and add 18% reducing agent (the composition is fixed carbon 86.47%, volatile matter 8.58%, ash 4.95%, S0.31%), flux (Na 2 SO 4 1.5%, CaF 2 2.5%) and binder (cornmeal 3.0%), mix thoroughly, add water, press into a block, dry at 200-300°C, add to the rotary hearth furnace for high temperature reduction, the temperature in the rotary hearth furnace Keep it at 1350-1500°C, and the reduction time is controlled at 15-45min. After the reduction, magnetic separation separates to obtain high-titanium slag and pearl iron. The iron content is less than 2%, which meets the raw material requirements of the sulfuric acid titanium dioxide production process; the iron content of pearl iron is more than 96%, which is a high-quality steelmaking raw material for electric furnaces. ...
PUM
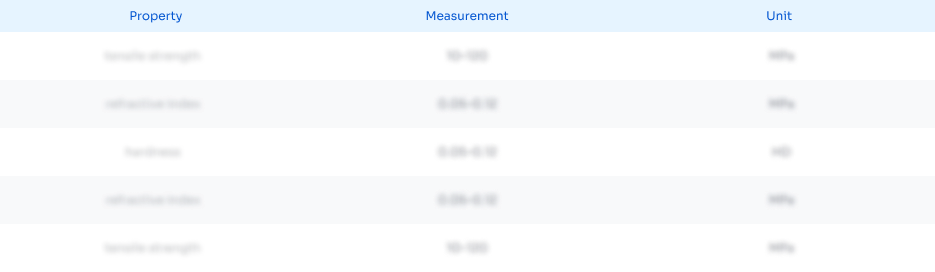
Abstract
Description
Claims
Application Information

- R&D
- Intellectual Property
- Life Sciences
- Materials
- Tech Scout
- Unparalleled Data Quality
- Higher Quality Content
- 60% Fewer Hallucinations
Browse by: Latest US Patents, China's latest patents, Technical Efficacy Thesaurus, Application Domain, Technology Topic, Popular Technical Reports.
© 2025 PatSnap. All rights reserved.Legal|Privacy policy|Modern Slavery Act Transparency Statement|Sitemap|About US| Contact US: help@patsnap.com