A kind of preparation method of trifluoroethylene and tetrafluoromethane
A technology of tetrafluoromethane and trifluoroethylene, which is applied in the field of preparation of trifluoroethylene and tetrafluoromethane, can solve the problems of high equipment requirements and achieve the effect of improving the conversion rate
- Summary
- Abstract
- Description
- Claims
- Application Information
AI Technical Summary
Problems solved by technology
Method used
Image
Examples
Embodiment 1
[0030] First, weigh Cr(NO 3 ) 3 and Al(NO 3 ) 3 , mix well with an appropriate amount of water, add a certain amount of ammonium carbonate to Cr 3+ and Al 3+ After the precipitation is complete, it is separated and washed until the solution is neutral, and then dried at 120°C for 12 hours. The dried precipitate was calcined at 400°C in an air atmosphere for 6 hours, and pressed into tablets to obtain the catalyst precursor (Cr 2 o 3 -Al 2 o 3 ), then use N 2 The gas was dried at 300°C for 5 hours, and then treated with anhydrous HF at 350°C for 5 hours to obtain a fluorination catalyst (Cr 2 o 3 -AlF 3 ).
[0031] refer to figure 1 : A certain amount of above-mentioned fluorination catalyst is added in the reactor I, press CFC-12 and HFC-134a molar ratio 1: 4, at temperature 450 ℃, normal pressure, space velocity 800h -1 The reaction is carried out under the following conditions; the gas after the reaction is separated by separation tower I, and the separated HFC...
Embodiment 2
[0034] First, weigh Cr(NO 3 ) 3 and Mg(NO 3 ) 2 , mix evenly with an appropriate amount of water, add a certain amount of ammonia water to make Cr 3+ and Mg 2+ After the precipitation is complete, it is separated and washed until the solution is neutral, and then dried at 150°C for 10 hours. The dried precipitate was calcined at 400°C in an air atmosphere for 6 hours, and pressed into tablets to obtain the catalyst precursor (Cr 2 o 3-MgO), then use N 2 The gas was dried at 300°C for 10 hours, and then treated with anhydrous HF at 400°C for 5 hours to obtain a fluorination catalyst (Cr 2 o 3 -MgF 2 )
[0035] refer to figure 1 : A certain amount of above-mentioned fluorination catalyst is added in the reactor I, press CFC-12 and HFC-134a molar ratio 1: 2, at temperature 450 ℃, normal pressure, space velocity 700h -1 The reaction is carried out under the following conditions; the gas after the reaction is separated by separation tower I, and the separated HFC-134a, ...
Embodiment 3
[0038] First, weigh Cr(NO 3 ) 3 and Y(NO 3 ) 3 , mix well with an appropriate amount of water, add a certain amount of ammonium carbonate to Cr 3+ and Y 3+ After the precipitation is complete, it is separated and washed until the solution is neutral, and then dried at 120°C for 10 hours. After the dried precipitate was shaped, it was baked at 600 ° C for 5 hours in a nitrogen atmosphere, and pressed into tablets, that is, to the catalyst precursor (Cr 2 o 3 -Y 2 o 3 ), then use N 2 The gas was dried at 400°C for 3 hours, and then treated with anhydrous HF at 450°C for 8 hours to obtain a fluorination catalyst (Cr 2 o 3 -YF 3 ).
[0039] refer to figure 1 : A certain amount of above-mentioned fluorination catalyst is added in the reactor I, press CFC-12 and HFC-134a molar ratio 1: 9, at temperature 500 ℃, normal pressure, space velocity 1500h -1 The reaction is carried out under the following conditions; the gas after the reaction is separated by separation tower ...
PUM
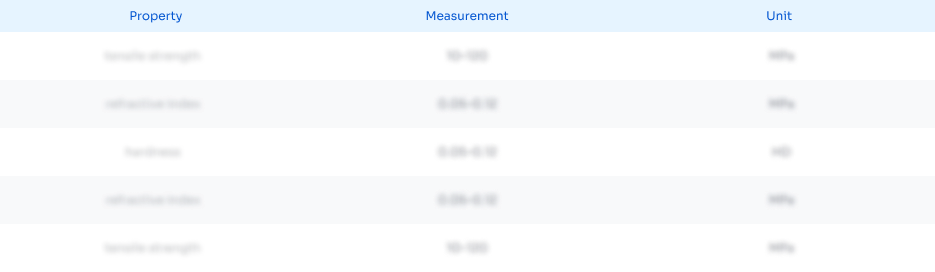
Abstract
Description
Claims
Application Information

- Generate Ideas
- Intellectual Property
- Life Sciences
- Materials
- Tech Scout
- Unparalleled Data Quality
- Higher Quality Content
- 60% Fewer Hallucinations
Browse by: Latest US Patents, China's latest patents, Technical Efficacy Thesaurus, Application Domain, Technology Topic, Popular Technical Reports.
© 2025 PatSnap. All rights reserved.Legal|Privacy policy|Modern Slavery Act Transparency Statement|Sitemap|About US| Contact US: help@patsnap.com