Junction box of solar photovoltaic module
A solar photovoltaic and junction box technology, which is applied in the field of solar photovoltaic module junction boxes, can solve the problems of shortening the service life of junction boxes, aging cracks, poor heat dissipation of junction boxes, etc., and achieves improved stability and photoelectric conversion efficiency, high voltage resistance and electrical conductivity The effect of strengthening capacity and facilitating automatic production and processing
- Summary
- Abstract
- Description
- Claims
- Application Information
AI Technical Summary
Problems solved by technology
Method used
Image
Examples
Embodiment Construction
[0034] Specific embodiments of the present invention will be further described in detail below.
[0035] like Figure 1~5 Shown, the present invention comprises electric part 2, and electric part 2 comprises a group of metal sheets 201 and the diode 202 that is connected between metal sheets 201, and cable 3 connects two sheet metal sheets 201 of electric part 2 both sides, and connection mode can be by The tail ends 205 of the metal sheets 201 on the left and right sides of the electrical part 2 are bent and tightly wrapped around the cable 3. The number of metal sheets 201 and diodes 202 is determined according to different requirements. In this embodiment, the electrical part 2 includes 4 metal sheets 201 and three diodes 201 connected in series between four metal sheets 201, the metal sheet 201 is a copper sheet, the diode 202 is a patch diode, and the metal sheet 201 is extended with an integral heat sink 203, so that the metal sheet 201 As a conductive component, it als...
PUM
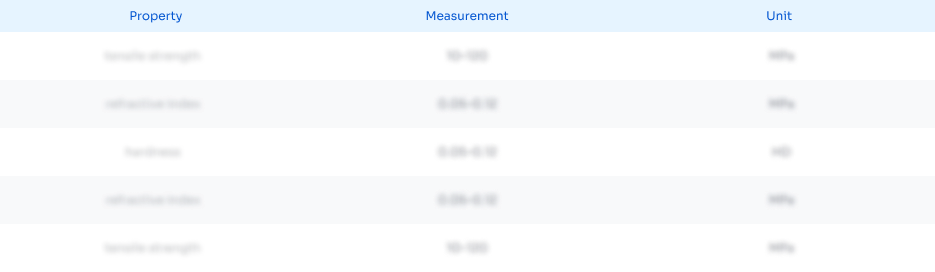
Abstract
Description
Claims
Application Information

- R&D
- Intellectual Property
- Life Sciences
- Materials
- Tech Scout
- Unparalleled Data Quality
- Higher Quality Content
- 60% Fewer Hallucinations
Browse by: Latest US Patents, China's latest patents, Technical Efficacy Thesaurus, Application Domain, Technology Topic, Popular Technical Reports.
© 2025 PatSnap. All rights reserved.Legal|Privacy policy|Modern Slavery Act Transparency Statement|Sitemap|About US| Contact US: help@patsnap.com