Modification method of lignin
A lignin modification technology, applied in the field of lignin, can solve the problems of high process requirements, achieve the effects of improving reactivity, facilitating commercialization, and facilitating packaging and transportation
- Summary
- Abstract
- Description
- Claims
- Application Information
AI Technical Summary
Problems solved by technology
Method used
Image
Examples
Embodiment 1
[0031] Lignosulfonate: sodium hydroxide: n-dodecanethiol: dimethylformamide (mass ratio) is 1:0.2:1:5. Stir n-dodecanethiol, a part of dimethylformamide and sodium hydroxide at room temperature for 20 minutes, dissolve lignosulfonate in the remaining solvent, stir for 10 minutes, add the solution containing lignosulfonate To the mixture containing n-dodecanethiol and sodium hydroxide. Oil bath at 130°C, reacted for 3h under nitrogen protection. After the reaction is completed, add water to dilute and add acid to adjust the pH to 2, centrifuge to obtain demethylated lignin, dry at room temperature, wash with n-hexane, filter, and dry at room temperature again to obtain demethylated lignin.
[0032]
Embodiment 2
[0034] Lignosulfonate: sodium hydroxide: n-dodecanethiol: ethyl acetate (mass ratio) is 1:0.3:1:5. Stir n-dodecanethiol, a part of dimethylformamide and sodium methoxide at room temperature for 20 minutes, dissolve the lignosulfonate in the remaining ethyl acetate solvent, stir for 10 minutes, and dissolve the solution containing lignosulfonate Added to the mixture containing n-dodecanethiol and sodium methoxide. Oil bath at 100°C, under nitrogen protection, react for 1h. After the reaction is completed, add water to dilute and add acid to adjust the pH to 2, centrifuge to obtain demethylated lignin, dry at room temperature, wash with n-hexane, filter, and dry at room temperature again to obtain demethylated lignin.
[0035] The organic solvent used is any one of dimethylformamide, ethyl acetate, dioxane, pyridine or methanol or any mixture of any several
Embodiment 3
[0037]Alkali lignin: potassium tert-butoxide: n-decamercaptan: methanol (mass ratio) is 1:0.6:1.5:5. Stir n-decathiol, a part of dimethylformamide and sodium methoxide at room temperature for 20 minutes, dissolve the alkali lignin in the remaining solvent, stir for 10 minutes, add the solution containing n-decathiol and methanol sodium mixture. Oil bath at 120°C, reacted for 1.5h under nitrogen protection. After the reaction is completed, add water to dilute and add acid to adjust the pH to 2, centrifuge to obtain demethylated lignin, dry at room temperature, wash with n-hexane, filter, and dry at room temperature again to obtain demethylated lignin.
[0038]
PUM
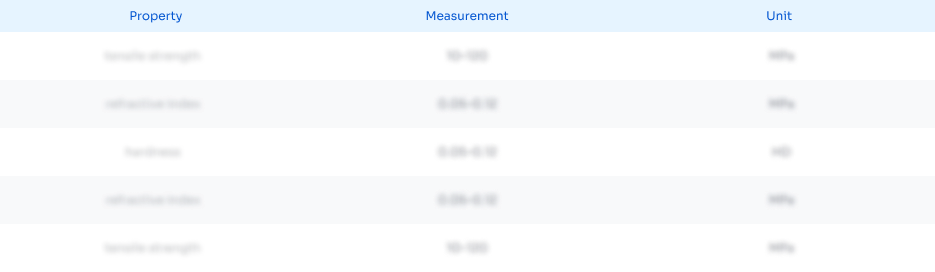
Abstract
Description
Claims
Application Information

- R&D Engineer
- R&D Manager
- IP Professional
- Industry Leading Data Capabilities
- Powerful AI technology
- Patent DNA Extraction
Browse by: Latest US Patents, China's latest patents, Technical Efficacy Thesaurus, Application Domain, Technology Topic, Popular Technical Reports.
© 2024 PatSnap. All rights reserved.Legal|Privacy policy|Modern Slavery Act Transparency Statement|Sitemap|About US| Contact US: help@patsnap.com