Method for producing steel-plastic multi-element composite pipes
A production method and multi-component composite technology, applied in the direction of pipes, rigid pipes, tubular objects, etc., can solve the problems of poor rigidity and temperature resistance, easy to rust, can not be used for oil transportation and high-pressure water transportation, and achieve anti-crack performance Increase, prevent rust, improve the effect of resistance to longitudinal force and deformation resistance
- Summary
- Abstract
- Description
- Claims
- Application Information
AI Technical Summary
Problems solved by technology
Method used
Image
Examples
Embodiment Construction
[0023] Below in conjunction with all accompanying drawings, the present invention will be further described. A preferred embodiment of the present invention is: the production method of the steel-plastic multi-component composite pipe described in this embodiment includes the following steps:
[0024] Step 1: Reinforce and toughen HDPE or PVC plastic through modification equipment, and make it into a plastic strip 1;
[0025] The second step: the steel strip is rolled by rolling equipment to form a hollow reinforcing rib 2 with both sides concave and overlapped; The cross-section of the rib can be square, trapezoidal, arc-shaped or triangular; it can also be designed into other geometric shapes as required. Fixed hook 3 is used for fixing the cement slurry after solidification.
[0026] The third step: use continuous welding equipment to weld the notch at the bottom of the reinforcing rib to make the reinforcing rib form a whole;
[0027] The fourth step: use spiral winding ...
PUM
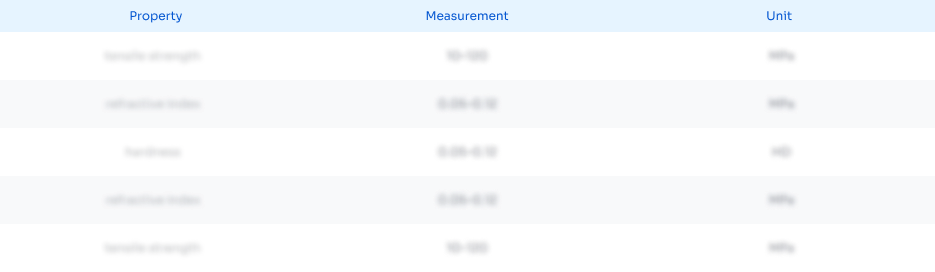
Abstract
Description
Claims
Application Information

- R&D
- Intellectual Property
- Life Sciences
- Materials
- Tech Scout
- Unparalleled Data Quality
- Higher Quality Content
- 60% Fewer Hallucinations
Browse by: Latest US Patents, China's latest patents, Technical Efficacy Thesaurus, Application Domain, Technology Topic, Popular Technical Reports.
© 2025 PatSnap. All rights reserved.Legal|Privacy policy|Modern Slavery Act Transparency Statement|Sitemap|About US| Contact US: help@patsnap.com