Method for zinc raw material dechlorination in zinc hydrometallurgy
A technology of hydrometallurgy and raw materials, applied in the field of hydrometallurgy, can solve the problems such as inability to dechlorinate treatment, achieve good dechlorination effect, no environmental pollution, and increase the effect of waste residue
- Summary
- Abstract
- Description
- Claims
- Application Information
AI Technical Summary
Problems solved by technology
Method used
Image
Examples
Embodiment 1
[0029] A method for dechlorination of zinc-containing raw materials in zinc hydrometallurgy, specifically comprising the following sequential steps, ①. Ball milling process: 10 tons of high-chlorine zinc-containing raw materials (the mass percentage of chlorine is 2.5%) are ball-milled with a drum ball mill and added with water to form a slurry. After ball-milling, samples are taken so that they can pass through an 80-mesh sieve; ②. Washing process: pump the ball mill slurry in step ① into the washing tank, add 100 m 3 Water, the liquid-solid mass ratio of water and the material in the slurry is 10.0:1, and the slurry is stirred and washed at a temperature of 30°C for 120 minutes, and the chlorine content in the solution is 1.85g / L. The zinc content in the medium is 2.45g / L. After washing, filter, the filtrate enters the zinc precipitation tank, and the filter residue is sampled. The chlorine mass percentage in the dry residue is 0.65%, and the filter residue enters the neutra...
Embodiment 2
[0032] A method for dechlorination of zinc-containing raw materials in zinc hydrometallurgy, specifically comprising the following sequential steps, ①. Ball milling process: 10 tons of high-chlorine zinc-containing raw materials (the mass percentage of chlorine is 2.5%) are ball-milled with a drum ball mill and added with water to form a slurry. After ball-milling, samples are taken so that they can pass through an 80-mesh sieve; ②. Washing process: pump the ball mill slurry in step ① into the washing tank, add 60m 3Water, the liquid-solid mass ratio of water and the material in the slurry is 6.0:1, and the slurry is stirred and washed at a temperature of 50°C for 150 minutes, and the chlorine content in the solution is 3.32g / L. The zinc content in the medium is 4.07g / L. After washing and filtering, the filtrate enters the zinc precipitation tank, and the filter residue is sampled. The chlorine mass percentage in the dry residue is 0.51%, and the filter residue enters the neut...
Embodiment 3
[0035] A method for dechlorination of zinc-containing raw materials in zinc hydrometallurgy, specifically comprising the following sequential steps, ①. Ball milling process: 10 tons of high-chlorine zinc-containing raw materials (the mass percentage of chlorine is 2.5%) are ball-milled with a drum ball mill and added with water to form a slurry. After ball-milling, samples are taken so that they can pass through an 80-mesh sieve; ②. Washing process: pump the ball mill slurry in step ① into the washing tank, add 40m 3 Water, the liquid-solid mass ratio of water and the material in the slurry is 4.0:1, and the slurry is stirred and washed at a temperature of 60°C for 180 minutes, and the chlorine content in the solution is 4.75g / L. The zinc content in the medium is 6.1g / L. After washing and filtering, the filtrate enters the zinc precipitation tank, and the filter residue is sampled. The chlorine mass percentage in the dry residue is 0.59%, and the filter residue enters the neut...
PUM
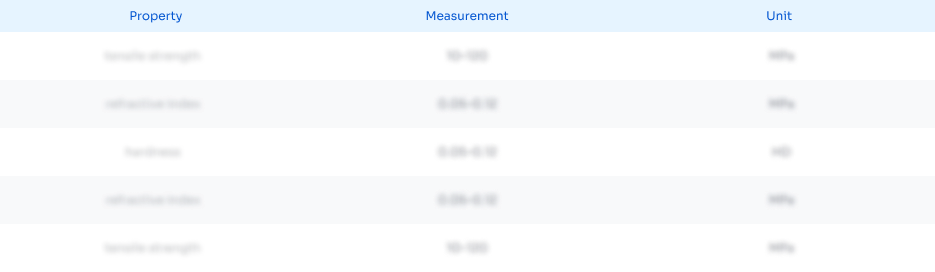
Abstract
Description
Claims
Application Information

- R&D
- Intellectual Property
- Life Sciences
- Materials
- Tech Scout
- Unparalleled Data Quality
- Higher Quality Content
- 60% Fewer Hallucinations
Browse by: Latest US Patents, China's latest patents, Technical Efficacy Thesaurus, Application Domain, Technology Topic, Popular Technical Reports.
© 2025 PatSnap. All rights reserved.Legal|Privacy policy|Modern Slavery Act Transparency Statement|Sitemap|About US| Contact US: help@patsnap.com