Method for producing energy-saving environmentally-friendly coal by using sludge
An energy-saving and environmentally friendly sludge technology, applied in sludge treatment, chemical instruments and methods, water/sludge/sewage treatment, etc., can solve the problems of unsatisfactory coal saving effect, high treatment cost, and large amount of pulverized coal consumption. Achieve the effects of reducing maintenance costs and spare parts loss, reducing environmental pollution, and large processing capacity
- Summary
- Abstract
- Description
- Claims
- Application Information
AI Technical Summary
Problems solved by technology
Method used
Examples
Embodiment 1
[0023] Example 1 The following steps are adopted to treat sludge and produce energy-saving and environment-friendly briquettes:
[0024] (1) Immediately add 3% (by weight of dehydrated sludge) of waste sulfuric acid to the dehydrated sludge, and add 15% (by weight of dehydrated sludge) of pure lime powder to mix and stir the dehydrated sludge. Deodorization treatment to obtain the dewatered sludge after deodorization for use;
[0025] (2) According to the proportion of 20% bituminous coal and 80% anthracite, take 200 kg of bituminous coal with 5500 kcal and 800 kg of anthracite with 6500 kcal as raw coal, mix and crush to obtain raw coal after crushing;
[0026] (3) Mix crushed raw coal with deodorized dewatered sludge with 10% raw coal weight, 0.5% raw coal weight alumina, 3% raw coal weight magnesium hydroxide, and 1% raw coal weight glass powder, and then add The red mud with 5% raw coal weight is mixed and stirred evenly, stacked and fermented at room temperature for 2 d...
Embodiment 2
[0027] Example 2 The following steps are adopted to treat sludge and produce energy-saving and environment-friendly briquettes:
[0028] (1) Immediately add 5% (by weight of dehydrated sludge) of waste hydrochloric acid to the dehydrated sludge, and add 10% (by weight of dehydrated sludge) of pure lime powder to mix and stir the dewatered sludge Deodorization treatment to obtain the dewatered sludge after deodorization for use;
[0029] (2) According to the proportion of 30% bituminous coal and 70% anthracite, take 300 kg of bituminous coal with 5600 kcal and 700 kg of anthracite with 6800 kcal as raw coal, mix and crush to obtain raw coal after crushing;
[0030] (3) Mix crushed raw coal with deodorized dewatered sludge with 20% weight of raw coal, alumina with 0.6% weight of raw coal, magnesium hydroxide with 6% weight of raw coal, glass powder with 2.5% weight of raw coal, and then add The red mud with 5% raw coal weight is mixed and stirred evenly, stacked and fermented...
Embodiment 3
[0031] Example 3 The following steps are adopted to treat sludge and produce energy-saving and environment-friendly briquettes:
[0032] (1) Immediately add 4% (by weight of dewatered sludge) of waste hydrochloric acid to the dehydrated sludge, and add 20% (by weight of dehydrated sludge) of pure lime powder to mix and stir the dewatered sludge. Deodorization treatment to obtain the dewatered sludge after deodorization for use;
[0033] (2) According to the proportion of 40% bituminous coal and 60% anthracite, take 400kg of bituminous coal with 5500 kcal and 600kg of anthracite with 6500 kcal as raw coal, mix and crush to obtain raw coal after crushing;
[0034] (3) Mix crushed raw coal with deodorized dewatered sludge with 10% raw coal weight, alumina with 0.8% raw coal weight, magnesium hydroxide with 5% raw coal weight, and glass powder with 2.8% raw coal weight, and then add The red mud with 6% raw coal weight is mixed and stirred evenly, piled up and fermented at room ...
PUM
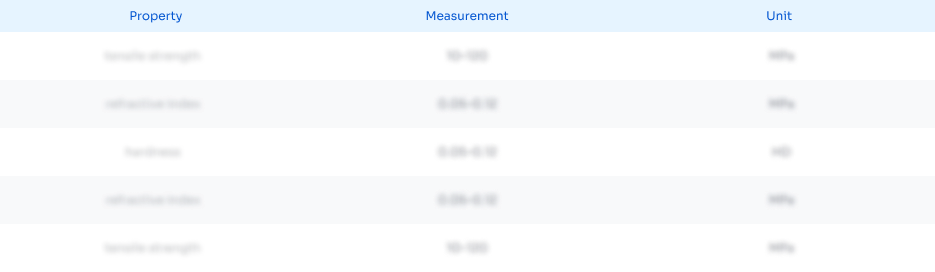
Abstract
Description
Claims
Application Information

- R&D
- Intellectual Property
- Life Sciences
- Materials
- Tech Scout
- Unparalleled Data Quality
- Higher Quality Content
- 60% Fewer Hallucinations
Browse by: Latest US Patents, China's latest patents, Technical Efficacy Thesaurus, Application Domain, Technology Topic, Popular Technical Reports.
© 2025 PatSnap. All rights reserved.Legal|Privacy policy|Modern Slavery Act Transparency Statement|Sitemap|About US| Contact US: help@patsnap.com