Method and device for purifying zinc sulfate solution based on action of cavitation effect
A technology of zinc sulfate solution and cavitation effect, applied in the direction of improving process efficiency, etc., can solve the problems of large zinc powder consumption, environmental pollution, high energy consumption, etc., and achieve reduced zinc powder unit consumption, low impurity content, and process flow shortened effect
- Summary
- Abstract
- Description
- Claims
- Application Information
AI Technical Summary
Problems solved by technology
Method used
Image
Examples
Embodiment 1
[0057] Embodiment 1: the zinc sulfate solution before purification containing impurity cadmium, cobalt, nickel, copper, its impurity content range is: Cd642.48mg / L, Cu18.33mg / L, Ni23.96mg / L, Co32.05mg / L. Adopt the purification process of three-stage cavitation effect to produce qualified new electrolytic solution, such as image 3 shown.
[0058] First, the temperature of the zinc sulfate solution is raised to 55-85°C through the heat exchanger 9, and the zinc powder is added to the slurry tank 1 in a conventional manner according to 1.0-1.4 times of the Cu+Cd impurity content in the zinc sulfate solution to be mixed with the zinc sulfate solution. , and then use the transfer pump 3 to inject the zinc sulfate solution after slurry adjustment into a section of purification tank 6 through a spray gun 4, and form cavitation bubbles due to the strong reflux effect caused by the barrier of the partition plate 5 in the tank, and react in a section of purification tank The time is 1...
Embodiment 2
[0062] Embodiment 2: the solution before zinc sulfate purification containing impurity cadmium, cobalt, nickel, copper, its impurity content range is: Cd454.55mg / L, Cu162.5mg / L, Ni12.5mg / L, Co37.5mg / L. The purification process using two-stage cavitation effect produces qualified new electrolytic solution, and zinc powder is added in the form of slurry. Such as image 3 shown.
[0063] First, the zinc sulfate solution is heated to 55-85°C through the heat exchanger 9, and the zinc powder is added to the slurry tank 1 in a conventional manner according to 1.0-1.4 times of the Cu+Cd impurity content in the solution to perform slurry mixing with the zinc sulfate solution, and then The delivery pump 3 is used to inject the zinc sulfate solution after pulp adjustment into the first-stage purification tank 6 through a spray gun 4 for a first-stage purification. The first-stage purification process is the process of removing copper and cadmium, and the temperature is 55-85°C; there ...
Embodiment 3
[0067] Embodiment 3: the zinc sulfate solution before purification containing impurity cadmium, cobalt, nickel, copper, its impurity content range is: Cd636.36mg / L, Cu62.5mg / L, Ni14.02mg / L, Co58mg / L. Two-stage purification process is adopted to produce qualified new electrolytic solution. Such as Figure 4 shown.
[0068] First, the temperature of the solution before zinc sulfate purification is raised to 55-85°C through the heat exchanger 9, and the zinc powder is added to the slurry mixing tank 1 according to 1.0-1.4 times of the Cu+Cd impurity content and 20-40 times of the Co+Ni content in the solution Slurry with zinc sulfate solution, add it in a conventional way, after high-speed stirring by the propeller blade stirring device 2 in tank 1, use the delivery pump 3 to transfer the zinc sulfate solution after slurry mixing to a section of purification tank 6, and pass through the propeller blade in tank 2 After the high-speed stirring of the stirring device 2, it interac...
PUM
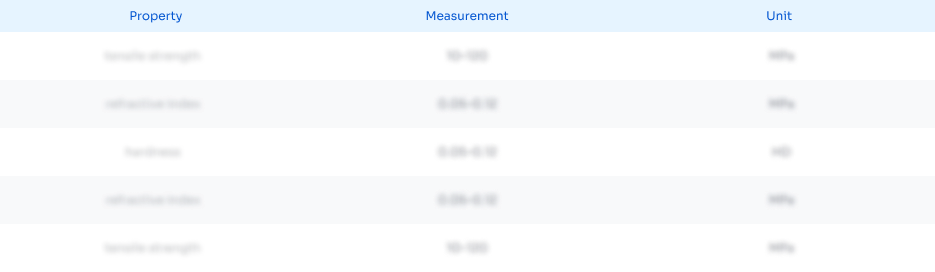
Abstract
Description
Claims
Application Information

- R&D Engineer
- R&D Manager
- IP Professional
- Industry Leading Data Capabilities
- Powerful AI technology
- Patent DNA Extraction
Browse by: Latest US Patents, China's latest patents, Technical Efficacy Thesaurus, Application Domain, Technology Topic, Popular Technical Reports.
© 2024 PatSnap. All rights reserved.Legal|Privacy policy|Modern Slavery Act Transparency Statement|Sitemap|About US| Contact US: help@patsnap.com