Electrolyte for melting aluminum foil of anode of capacitor and aluminum foil melting method
A technology of anode aluminum foil and chemical formation method, which is applied in the direction of electrolytic coating, surface reaction electrolytic coating, coating, etc., can solve the problems of low electrostatic capacity and withstand voltage value of anode foil, etc.
- Summary
- Abstract
- Description
- Claims
- Application Information
AI Technical Summary
Problems solved by technology
Method used
Image
Examples
Embodiment 1
[0071] Take the experimental results of 51Vf anode foil as an example:
[0072] (1) Turn the 20V sample into a film with a voltage of 23.8V and a specific volume of 75uF / cm 2 The corroded foil (using the method of EIAJ RC-2364A) is placed in the electrolyte solution containing 0.2% oxalic acid, 3.5% and deionized water, at a temperature of 65 ° C, 0.11A / dm 2 The electric current is treated for 100 seconds to obtain a first-grade formed foil.
[0073] (2) After cleaning the first-grade foil, put it into an 8% by weight ammonium adipate deionized aqueous solution, and at a temperature of 70°C, feed 0.16A / dm 2 The current is treated for 140 seconds to obtain a secondary formed foil.
[0074] (3) After cleaning the secondary foil, put it into 5.5% by weight ammonium adipate deionized aqueous solution, and pass through 0.17A / dm at a temperature of 70°C 2 The current is treated for 140 seconds to obtain a three-stage formed foil.
[0075] (4) After cleaning the tertiary formed f...
Embodiment 2
[0091] Take the experimental results of 142.0Vf anode foil as an example:
[0092] (1) Turn the 80V sample into a film with a voltage of 87.8V and a specific volume of 12.8uF / cm 2 The corroded foil (using the method of EIAJ RC-2364A) is placed in the electrolyte solution containing 0.6% oxalic acid, 5.25% ammonium adipate and ionized water. At a temperature of 75°C, 0.165A / dm 2 The electric current is treated for 140 seconds to obtain a first-grade formed foil.
[0093] (2) After cleaning the first-grade foil, put it into an 8% by weight ammonium adipate deionized aqueous solution, and at a temperature of 70°C, feed 0.16A / dm 2 The current is treated for 140 seconds to obtain a secondary formed foil.
[0094] (3) After cleaning the secondary foil, put it into 5.5% by weight ammonium adipate deionized aqueous solution, and pass through 0.17A / dm at a temperature of 70°C 2 The current is treated for 140 seconds to obtain a three-stage formed foil.
[0095] (4) After cleaning...
Embodiment 3
[0111] Take the experimental results of 150.0Vf anode foil as an example:
[0112] (1) Turn the 80V sample into a film with a voltage of 87.8V and a specific volume of 12.8uF / cm 2 The corroded foil (using the method of EIAJ RC-2364A) is placed in the electrolyte solution containing 1% oxalic acid, 7% ammonium adipate and ionized water. At a temperature of 85 ° C, 0.11A / dm 2 The electric current is treated for 180 seconds to obtain a first-grade formed foil.
[0113] (2) After cleaning the first-grade foil, put it into an 8% by weight ammonium adipate deionized aqueous solution, and at a temperature of 70°C, feed 0.16A / dm 2 The current is treated for 140 seconds to obtain a secondary formed foil.
[0114] (3) After cleaning the secondary foil, put it into 5.5% by weight ammonium adipate deionized aqueous solution, and pass through 0.17A / dm at a temperature of 70°C 2 The current is treated for 140 seconds to obtain a three-stage formed foil.
[0115] (4) After cleaning the...
PUM
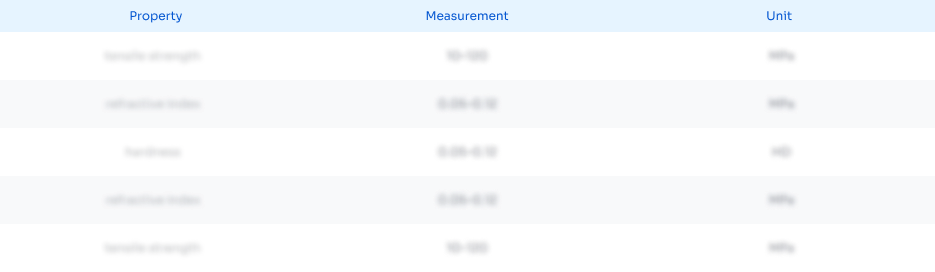
Abstract
Description
Claims
Application Information

- R&D
- Intellectual Property
- Life Sciences
- Materials
- Tech Scout
- Unparalleled Data Quality
- Higher Quality Content
- 60% Fewer Hallucinations
Browse by: Latest US Patents, China's latest patents, Technical Efficacy Thesaurus, Application Domain, Technology Topic, Popular Technical Reports.
© 2025 PatSnap. All rights reserved.Legal|Privacy policy|Modern Slavery Act Transparency Statement|Sitemap|About US| Contact US: help@patsnap.com