Stress-relaxation shaping method for complicated irregular-shaped integrated wallboard
A technology of stress relaxation and integral panel, which is applied in the direction of furnace type, furnace, heat treatment furnace, etc., can solve the problems of difficult manufacturing, long production cycle, and high processing cost of aircraft panel parts, so as to improve structural efficiency and shorten production cycle Effect
- Summary
- Abstract
- Description
- Claims
- Application Information
AI Technical Summary
Problems solved by technology
Method used
Image
Examples
Embodiment 1
[0028] This embodiment is used for forming (750×710) mm aircraft wing high-rib strip complex special-shaped integral wall panels. The mold used in the forming is an autoclave aging forming mold. The siding material is 2124-T85 aluminum alloy. The shaping process of the present embodiment comprises the following steps:
[0029] 1. Prepare materials. The materials to be prepared include: AT200Y is used for sealing putty with a working temperature of 204°C; the vacuum bag is made of WL7400 nylon vacuum film with a working temperature of 204°C, which has a melting point of 215°C; the air felt is Airweave N-10 with a working temperature of 204°C.
[0030] 2. Clean the mold and the panel to be formed. Degrease and clean the mold and the wall to be formed with acetone.
[0031] 3. Make vacuum bags. Position the siding blank on the mold and cover it with two layers of air felt; the position of the air felt should ensure that the outer surface of the mold is well wrapped, and add ...
Embodiment 2
[0039] This embodiment is used for forming (300×300) mm aircraft wing high-rib strips with complex and special-shaped integral wall panels. The mold used in the forming is an autoclave aging forming mold. Siding material 2124-T85 aluminum alloy. The concrete steps of this embodiment are as follows:
[0040] 1. Prepare materials. Materials to be prepared include: GS-213-3 for sealing putty with a service temperature of 232°C; vacuum bag with HK7400 nylon vacuum film with a service temperature of 210°C, which has a melting point of 220°C; air felt with AIRBLEED100 / 100GREY.
[0041] 2. Clean the mold and the panel to be formed. Degrease and clean the mold and the wall to be formed with acetone.
[0042] 3. Make vacuum bags. Position the siding blank on the mold and cover with three layers of air felt; the position of the air felt should ensure that the outer surface of the mold is well wrapped, and add two layers of air felt at the sharp corners and pores on the mold and t...
Embodiment 3
[0050] This embodiment is used for forming (500×500) mm aircraft wing high-rib strips with complex and special-shaped integral wall panels. The mold used in the forming is an autoclave aging forming mold. Siding material 2124-T85 aluminum alloy. The concrete steps of this embodiment are as follows:
[0051] 1. Prepare materials. The materials to be prepared include: SM5160 for sealing putty with a service temperature of 371°C; HK8400 nylon vacuum film with a service temperature of 232°C for the vacuum bag, which has a melting point of 260°C; AIRBLEED10HA with a service temperature of 205°C for the air felt.
[0052] 2. Clean the mold and the panel to be formed. Degrease and clean the mold and the wall to be formed with acetone.
[0053] 3. Make vacuum bags. Position the siding blank on the mold and cover with three layers of air felt; the position of the air felt should ensure that the outer surface of the mold is well wrapped, and add two layers of air felt at the sharp ...
PUM
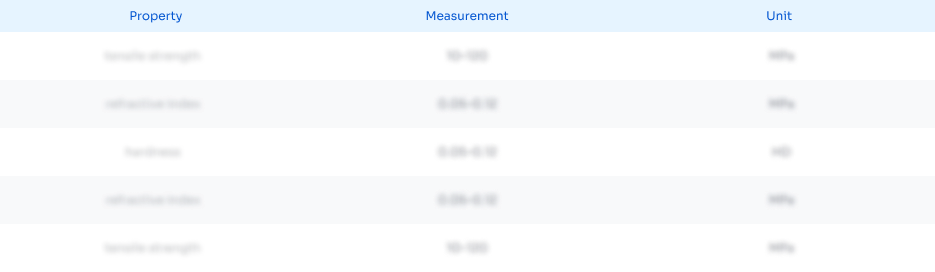
Abstract
Description
Claims
Application Information

- Generate Ideas
- Intellectual Property
- Life Sciences
- Materials
- Tech Scout
- Unparalleled Data Quality
- Higher Quality Content
- 60% Fewer Hallucinations
Browse by: Latest US Patents, China's latest patents, Technical Efficacy Thesaurus, Application Domain, Technology Topic, Popular Technical Reports.
© 2025 PatSnap. All rights reserved.Legal|Privacy policy|Modern Slavery Act Transparency Statement|Sitemap|About US| Contact US: help@patsnap.com