Method for lowering sulfur and olefin content in gasoline
A technology for olefin content and gasoline, which is applied in the field of producing clean gasoline components, and can solve problems such as reducing olefin content and sulfur content, and complex processes
- Summary
- Abstract
- Description
- Claims
- Application Information
AI Technical Summary
Problems solved by technology
Method used
Image
Examples
Embodiment 1
[0037] Gasoline feedstock with 40wt% olefin content (see Table 1 for properties) was contacted with adsorbent AZ-1 in a small continuous fluidized bed reactor for desulfurization reaction. The composition of AZ-1 is: Al 2 o 3 12.5%, SiO 2 10%, ZnO 55%, NiO 22.5%, the reaction conditions are: the reaction temperature is 400°C, the reactor pressure is 2.5Mpa, and the weight hourly space velocity of the gasoline raw material is 4h -1 , hydrogen is used as the hydrogen donor, and the volume ratio of hydrogen to gasoline raw materials is 70. The desulfurized product obtained from the top of the reactor is cooled and separated to obtain a liquid product. The regeneration temperature of the catalyst is 550°C, and the adsorbent is cooled to 340°C and returned to the reactor for recycling. The olefin content in the product gasoline was 25% by weight.
Embodiment 2
[0039] Gasoline feedstock with 40wt% olefin content (see Table 1 for properties) was contacted with adsorbent AZ-1 in a small continuous fluidized bed reactor for desulfurization reaction. The reaction conditions are: the reaction temperature is 430°C, the reactor pressure is 2.2Mpa, and the weight hourly space velocity of the gasoline raw material is 4h -1 , hydrogen is used as the hydrogen donor, and the volume ratio of hydrogen to gasoline raw materials is 100. The desulfurized product obtained from the top of the reactor is cooled and separated to obtain a liquid product. Part of the adsorbent is taken out from the middle and upper part of the reactor into the external heat extractor 9, and the heat is taken to cool down to 380°C, and then returned to the reactor through two inlets in the middle and lower part of the reactor for circulation, and the regeneration temperature of the catalyst is 550°C. The olefin content in the resulting product gasoline was 21% by weight. ...
Embodiment 3
[0041] This example illustrates the adsorbent A used in the pretreatment step and its preparation.
[0042] Extrude 400g of aluminum hydroxide powder (SB powder, product of Codea, Germany) into a φ1.4mm cylindrical strip on an extruder, dry the wet strip in an oven at 120°C for 2 hours, and then roast it in a tube furnace at 600°C with air 4 hours to obtain the vector.
[0043] 400gNi(CH 3 COO) 2 4H 2 O was dissolved with 18wt% ammonia water, the dissolved volume was 800ml, pH=9.0. Put 200 g of the aforementioned carrier in 400 ml of the solution and soak for 4 hours, and filter off the remaining soaking liquid. The dipped wet strips were dried in an oven at 120°C for 2 hours. Roast in air at 400° C. in a tube furnace for 4 hours, and the above impregnation and roasting are repeated twice. Afterwards, vulcanization is carried out at a pressure of 1.2MPa and a weight hourly space velocity of 10hr -1 , temperature is 290 ℃, under the condition that the volume ratio of hyd...
PUM
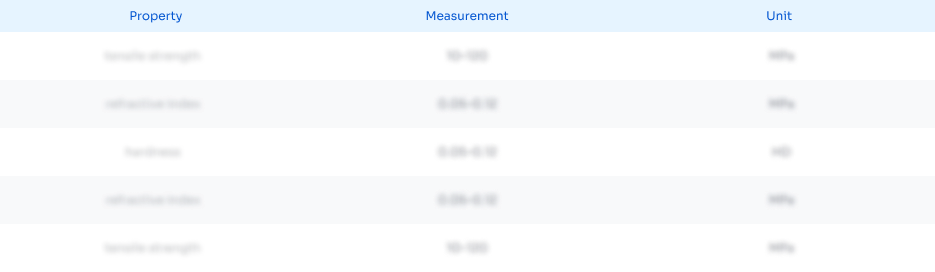
Abstract
Description
Claims
Application Information

- Generate Ideas
- Intellectual Property
- Life Sciences
- Materials
- Tech Scout
- Unparalleled Data Quality
- Higher Quality Content
- 60% Fewer Hallucinations
Browse by: Latest US Patents, China's latest patents, Technical Efficacy Thesaurus, Application Domain, Technology Topic, Popular Technical Reports.
© 2025 PatSnap. All rights reserved.Legal|Privacy policy|Modern Slavery Act Transparency Statement|Sitemap|About US| Contact US: help@patsnap.com