Radiating fin
A technology of heat sinks and heat dissipation fins, applied in cooling/ventilation/heating transformation, electrical components, electrical solid devices, etc. Simple and stable, improved heat dissipation performance, obvious effect of heat dissipation
- Summary
- Abstract
- Description
- Claims
- Application Information
AI Technical Summary
Problems solved by technology
Method used
Image
Examples
Embodiment Construction
[0014] The present invention will be further described in detail below with reference to the accompanying drawings and embodiments, and it should be understood that these embodiments are only used to illustrate the present invention and not to limit the scope of the present invention.
[0015] like figure 1 As shown, the heat sink includes a base 1 and a set of heat dissipation fins 2, the base 1 and the heat dissipation fins 2 are made of aluminum alloy materials with good thermal conductivity, and the heat dissipation fins 2 are punched by stamping Insert the base 1 and connect it firmly; due to punching, the upper surface of the base 1 and the heat dissipation fin 2 and the bottom surface of the base 1 will have depressions and protrusions respectively, and the protrusions can be punched or It is removed by grinding to maintain the flatness of the bottom surface, so that the base 1 is closely attached to the heat source, and the heat dissipation area is enlarged.
[0016] ...
PUM
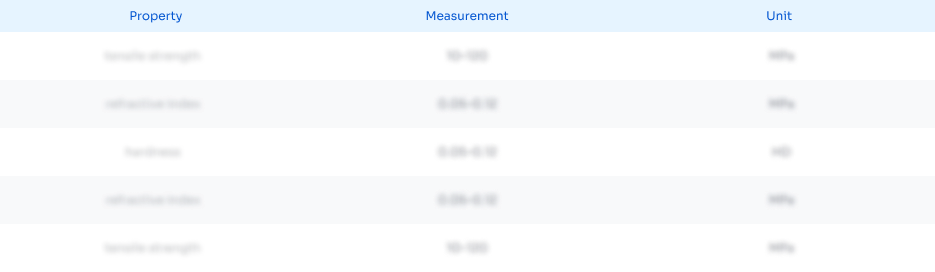
Abstract
Description
Claims
Application Information

- R&D Engineer
- R&D Manager
- IP Professional
- Industry Leading Data Capabilities
- Powerful AI technology
- Patent DNA Extraction
Browse by: Latest US Patents, China's latest patents, Technical Efficacy Thesaurus, Application Domain, Technology Topic, Popular Technical Reports.
© 2024 PatSnap. All rights reserved.Legal|Privacy policy|Modern Slavery Act Transparency Statement|Sitemap|About US| Contact US: help@patsnap.com