Environment-friendly biological texture etch solution and application method thereof
A bio-environmental protection and application method technology, applied in chemical instruments and methods, crystal growth, final product manufacturing, etc., can solve the problems of uneven quality of isopropanol, endanger the survival of all species, easily pollute the working environment, etc., and achieve raw material Stable source, good storage stability, good reproducible effect
- Summary
- Abstract
- Description
- Claims
- Application Information
AI Technical Summary
Problems solved by technology
Method used
Examples
Embodiment 1
[0023] First pour 8.6kg of deionized water into the cleaned texture tank, and add 0.5kg of sodium citrate, 0.9kg of anhydrous sodium carbonate and 20ppm of alkyl glycoside BG-10 respectively during the stirring process. Stir evenly to prepare a bio-environmentally friendly texturing solution, which is heated to 80°C. Take the cut monocrystalline silicon wafer and put it into an ultrasonic tank filled with deionized water for 10 minutes, and then put the silicon wafer into the texturing tank for texturing for 25 minutes. Finally, the silicon wafer was taken out and placed in an ultrasonic tank filled with deionized water for ultrasonic rinsing for 10 minutes.
[0024] After the solar single chip is textured by the above-mentioned texturing liquid, the obtained texture pyramid is small, uniform, and has a high coverage rate, and the quality difference before and after the monolithic texture is 0.4g.
Embodiment 2
[0026] First pour 9.5kg of deionized water into the cleaned velvet tank, and add 0.2kg of sodium citrate, 0.3kg of anhydrous sodium carbonate and 10ppm of alkyl glycoside APG1214 respectively during the stirring process. Stir evenly to prepare a bio-environmental-friendly texturing solution, which is heated to 85°C. Take the cut monocrystalline silicon wafer and put it into an ultrasonic tank filled with deionized water for 15 minutes, and then put the silicon wafer into the texturing tank for texturing for 30 minutes. Finally, the silicon wafer was taken out and placed in an ultrasonic tank filled with deionized water for ultrasonic rinsing for 15 minutes.
[0027] After the solar single chip is textured by the above texturing liquid, the textured pyramid obtained is small, uniform, and has a high coverage rate, and the quality difference before and after the monolithic texture is 0.1g.
Embodiment 3
[0029] First pour 7.7kg of deionized water into the cleaned texture tank, and add 0.8kg of sodium citrate, 1.5kg of anhydrous sodium carbonate and 80ppm of alkyl glycoside BG-10 respectively during the stirring process. Stir evenly to prepare a bio-environmental-friendly texturing liquid, which is heated to 75°C. Take the cut monocrystalline silicon wafer and put it into an ultrasonic tank filled with deionized water for 5 minutes, and then put the silicon wafer into the texturing tank for 10 minutes of texturing. Finally, the silicon wafer was taken out and placed in an ultrasonic tank filled with deionized water for ultrasonic rinsing for 5 minutes.
[0030] After the solar single chip is textured by the above texturing liquid, the obtained texture pyramid is small, uniform, and has a high coverage rate, and the quality difference before and after the monolithic texture is 1.0g.
PUM
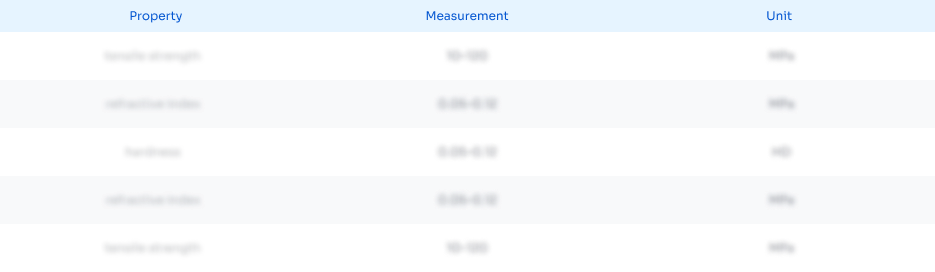
Abstract
Description
Claims
Application Information

- R&D
- Intellectual Property
- Life Sciences
- Materials
- Tech Scout
- Unparalleled Data Quality
- Higher Quality Content
- 60% Fewer Hallucinations
Browse by: Latest US Patents, China's latest patents, Technical Efficacy Thesaurus, Application Domain, Technology Topic, Popular Technical Reports.
© 2025 PatSnap. All rights reserved.Legal|Privacy policy|Modern Slavery Act Transparency Statement|Sitemap|About US| Contact US: help@patsnap.com