Oil shale waste residue haydite and preparation method thereof
A technology of oil shale waste residue and shale waste residue, which is applied in the field of oil shale waste residue ceramsite and its preparation, can solve the problems of pollution, land occupation, etc., and achieve the effects of avoiding a large amount of accumulation, reducing environmental pollution, and increasing economic benefits
- Summary
- Abstract
- Description
- Claims
- Application Information
AI Technical Summary
Problems solved by technology
Method used
Examples
Embodiment 1
[0018] ① Take oil 200 mesh oil shale residue 3000g, green shale 1850g, admixture 150g, put it into a ball mill and grind it for 35 minutes, and grind it into a 200 mesh mixture fine powder for later use;
[0019] ② Evenly mix the fine powder of the mixture with 900g of water, and use a ball forming plate to make raw meal balls;
[0020] ③ Dry the raw meal balls naturally for 24 hours;
[0021] ④Put the naturally dried raw meal balls into a drying oven and dry them at 100°C for 8 hours;
[0022] ⑤Put the dried raw meal balls into a continuous simulated industrial experimental furnace for calcination under a reducing atmosphere. The pre-calcination temperature is 700°C, and the preheating time is 20 minutes; the roasting temperature is 1180°C, and the roasting time is 15 minutes. finished product.
Embodiment 2
[0024] ①Take 3000g of 200-mesh oil shale waste residue, 250g of activated oil shale waste residue, 1500g of green shale, and 250g of admixture, put it into a ball mill for grinding for 35 minutes, and grind it into a 300-mesh mixture fine powder for later use;
[0025] ② Evenly mix the fine powder of the mixture with 1200g of water, and use a ball forming plate to make raw material balls;
[0026] ③ Dry the raw meal balls naturally for 24 hours;
[0027] ④Put the naturally dried raw meal balls into a drying oven and dry them at 100°C for 8 hours;
[0028] ⑤Put the dried raw meal balls into a continuous simulated industrial experimental furnace for calcination under a reducing atmosphere. The pre-calcination temperature is 500°C, and the preheating time is 15 minutes; the roasting temperature is 1150°C, and the roasting time is 20 minutes. finished product.
PUM
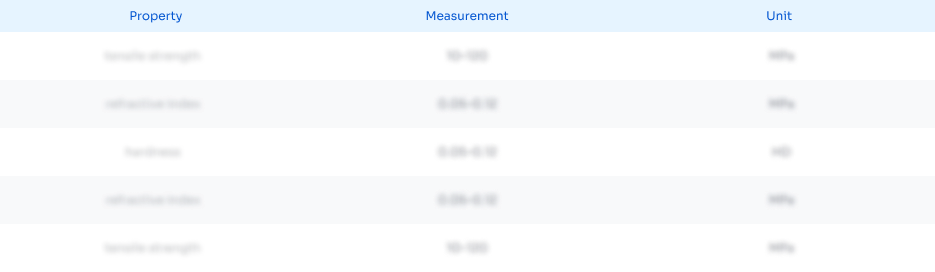
Abstract
Description
Claims
Application Information

- R&D
- Intellectual Property
- Life Sciences
- Materials
- Tech Scout
- Unparalleled Data Quality
- Higher Quality Content
- 60% Fewer Hallucinations
Browse by: Latest US Patents, China's latest patents, Technical Efficacy Thesaurus, Application Domain, Technology Topic, Popular Technical Reports.
© 2025 PatSnap. All rights reserved.Legal|Privacy policy|Modern Slavery Act Transparency Statement|Sitemap|About US| Contact US: help@patsnap.com