Preparation method of novel phosphorus-containing biphenyl novolac epoxy resin and condensate of novel phosphorus-containing biphenyl novolac epoxy resin
A technology of biphenyl novolac epoxy resin and phenol novolac epoxy resin, which is applied in the chemical industry, can solve the problems of corrosion of electronic components, dissociation of halides, human body harm, etc., and achieves low water absorption, excellent heat resistance and flame retardancy. The effect is simple and easy to operate
- Summary
- Abstract
- Description
- Claims
- Application Information
AI Technical Summary
Problems solved by technology
Method used
Image
Examples
Embodiment 1
[0063] like figure 1 As shown, the process route of this embodiment is as shown in the figure.
[0064] Step 1, add 24.2 parts of 4,4'-biphenyl dimethyl dimethyl ether and 87 parts of methyl butyl ketone in a four-necked flask with a thermometer, a stirring device and a condenser. Add 34 parts of p-phenylbiphenol into a four-necked flask in batches, stir and raise the temperature to 135°C, and maintain the reaction for 4 hours to remove methyl butyl ketone to obtain a biphenol-formaldehyde resin.
[0065] Step 2: add 15 parts of biphenyl novolac resins, 42.4 parts of epoxy chlorohydrin and 2.28 parts of NaOH solution (biphenyl novolac resins: epoxy chlorohydrin: hydroxide Sodium molar ratio 1:10:1), reacted at 65°C for 4h. Afterwards, the organic layer was taken by liquid separation, and the solvent was removed under reduced pressure to obtain the product.
[0066] Step 3, add 6 parts of biphenyl novolac epoxy resins, 1.94 parts of 10-(2,5-dihydroxyphenyl)-10-dihydro-9- Ox...
Embodiment 2
[0072] Step 1, add 24.2 parts of 4,4'-biphenyl dimethyl dimethyl ether and 87 parts of dichloroethane in a four-necked flask with a thermometer, a stirring device and a condenser. Add 34 parts of p-phenylbiphenol into the reaction bottle in batches, stir and raise the temperature to 80°C, and maintain the reaction for 8 hours, and discharge while hot to obtain biphenol novolac resin.
[0073] Step 2: add 15 parts of biphenyl phenolic resins, 53.01 parts of epoxy chlorohydrin and 2.28 parts of sodium hydroxide (biphenyl phenolic resins: epoxy chlorohydrin: hydrogen Sodium oxide molar ratio 1:10:1), react at 65°C for 4h, separate the liquid to take the organic layer, and remove the solvent under reduced pressure to obtain the product.
[0074] Step 3, add 6 parts of biphenyl novolac epoxy resin, 1.46 parts of 10-(2,5-dihydroxyphenyl)-10-dihydro-9- Oxa-10-phosphaphenanthrene-10-oxide (biphenol novolac epoxy resin and 10-(2,5-dihydroxyphenyl)-10-dihydro-9-oxa-10-phosphaphenanthre...
Embodiment 3
[0076] Step 1, add 24.2 parts of 4,4'-biphenyl dimethyl dimethyl ether and 87 parts of methyl isobutyl ketone in a four-necked flask with a thermometer, a stirring device and a condenser tube, and 34 parts of p-phenyl biphenyl Phenol was added to the reaction flask in batches, and the temperature was raised to 115°C with stirring, and the reaction was maintained for 5 hours, and the solvent was removed to obtain a biphenol-formaldehyde resin.
[0077] Step 2: add 15 parts of biphenyl phenolic resins, 63.62 parts of epoxy chlorohydrin and 2.28 parts of sodium hydroxide (biphenyl phenolic resins: epoxy chlorohydrin: hydrogen Sodium oxide molar ratio (1:12:1), react at 75°C for 4h, separate liquid to take the organic layer, and remove the solvent under reduced pressure to obtain the product.
[0078] Step 3, add 6 parts of biphenol novolac epoxy resin, 2.18 parts of 10-(2,5-dihydroxyphenyl)-10-dihydro-9- Oxa-10-phosphaphenanthrene-10-oxide (biphenol novolac epoxy resin and 10-(2...
PUM
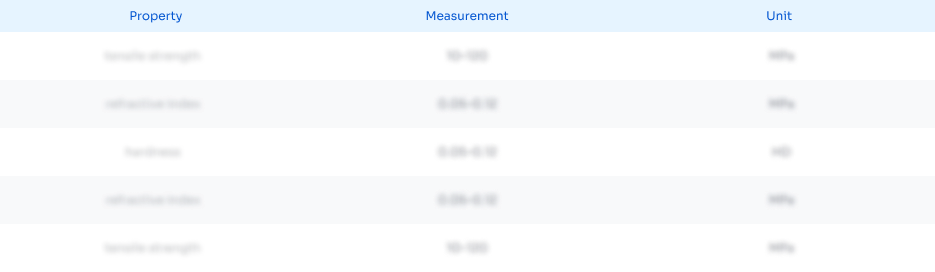
Abstract
Description
Claims
Application Information

- R&D
- Intellectual Property
- Life Sciences
- Materials
- Tech Scout
- Unparalleled Data Quality
- Higher Quality Content
- 60% Fewer Hallucinations
Browse by: Latest US Patents, China's latest patents, Technical Efficacy Thesaurus, Application Domain, Technology Topic, Popular Technical Reports.
© 2025 PatSnap. All rights reserved.Legal|Privacy policy|Modern Slavery Act Transparency Statement|Sitemap|About US| Contact US: help@patsnap.com