Molybdenum-tungsten separating process for molybdenum-tungsten mixed ammonium salt solution in tungsten hydrometallurgy
A technology of ammonium salt solution and solid-liquid separation, applied in the direction of improving process efficiency, etc., can solve problems such as difficulty in filtration, and achieve the effect of coarse and regular crystal structure
- Summary
- Abstract
- Description
- Claims
- Application Information
AI Technical Summary
Problems solved by technology
Method used
Examples
Embodiment 1
[0022] The raw material liquid is molybdenum and tungsten mixed ammonium salt solution recovered by ion exchange method, wherein WO 3 4.31g / l, Mo23.52g / l, with (NH 4 ) 2 S solution as vulcanizing agent, S 2- The ion excess coefficient is 1.03, vulcanized at room temperature for 48 hours, and left to crystallize at +4°C for 24 hours. The concentration of molybdenum in the mother liquor is 4.85g / l, and the molybdenum crystallization rate is 71.06%.
Embodiment 2
[0024] Raw material solution and vulcanization process parameter are the same as embodiment 1, add solid ammonium chloride as salting-out agent, and its addition is that every liter of solution adds 1.0molNH 4 Cl, the sulfidation solution was crystallized at +4°C for 18 hours, the molybdenum concentration in the mother liquor was 2.22g / l, and the molybdenum crystallization rate was 86.75%.
Embodiment 3
[0026] Alkaline tungsten stripping solution, WO 3 163.49g / l, Mo 6.55g / l, adding high-concentration ammonium molybdate solution, formulated to contain WO 3 151.38g / l, the ammonium tungstate solution of Mo 22.42g / l is the raw material solution, with (NH 4 ) 2 S solution as vulcanizing agent, S 2- The ion excess coefficient is 1.09, vulcanized at room temperature for 48 hours, standing at +4°C for 39 hours to crystallize, the concentration of molybdenum in the mother liquor is reduced to 4.81g / l, and the crystallization rate of molybdenum is 69.75%.
PUM
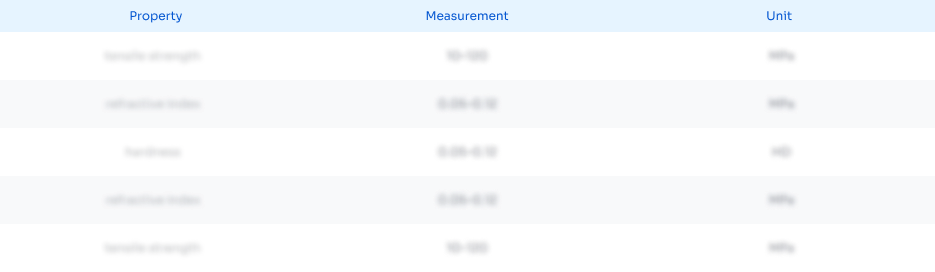
Abstract
Description
Claims
Application Information

- R&D
- Intellectual Property
- Life Sciences
- Materials
- Tech Scout
- Unparalleled Data Quality
- Higher Quality Content
- 60% Fewer Hallucinations
Browse by: Latest US Patents, China's latest patents, Technical Efficacy Thesaurus, Application Domain, Technology Topic, Popular Technical Reports.
© 2025 PatSnap. All rights reserved.Legal|Privacy policy|Modern Slavery Act Transparency Statement|Sitemap|About US| Contact US: help@patsnap.com