Buoy communication cable sheath rubber for ship and manufacturing method thereof
A technology for communication cables and manufacturing methods, which is applied to communication cables, rubber insulators, cables, etc., can solve problems such as short service life, and achieve the effects of good compactness, strong water resistance, and superior mechanical properties
- Summary
- Abstract
- Description
- Claims
- Application Information
AI Technical Summary
Problems solved by technology
Method used
Image
Examples
Embodiment 1
[0017] The manufacturing steps of sheath rubber are as follows:
[0018] (1) Prepare raw materials according to the following components and weight content: Chlorosulfonated polyethylene Haplon-40: 20 parts; Magnesium oxide: 1 part; Huangdan masterbatch: 3.5 parts; Paraffin wax: 0.5 parts; coumarone: 0.5 parts; antimony trioxide: 1.5 parts; dioctyl phthalate (DOP): 2.5 parts; semi-reinforcing carbon black: 5.0 parts; talcum powder: 4.5 parts; Methylenethiuram (DPTT): 0.3 parts; Dibenzothiazole disulfide (DM): 0.4 parts; Nickel dibutyldithiocarbamate (NBC): 0.2 parts;
[0019] (2) Mix chlorosulfonated polyethylene Haplon-40 for 3 minutes, then add magnesium oxide, yellow lead masterbatch, paraffin, polyethylene glycol, coumarone, antimony trioxide, and dioctyl phthalate Ester, semi-reinforcing carbon black, and talcum powder were mixed for 6 minutes to make the mixture evenly stirred; Then knead for another 30 seconds; then move the mixture to an open mill for sheeting to dis...
Embodiment 2
[0028] The manufacturing steps of sheath rubber are as follows:
[0029] (1) Prepare raw materials according to the following components and weight content: chlorosulfonated polyethylene Haplon-40: 20 parts; Magnesium oxide: 1.5 parts; Huangdan masterbatch: 4.5 parts; Paraffin wax: 1 part; Polyethylene glycol: 1 part coumarone: 1 part; antimony trioxide: 2 parts; dioctyl phthalate: 3 parts; semi-reinforcing carbon black: 6.5 parts; talcum powder: 6 parts; Lamb: 0.5 parts; Dibenzothiazole disulfide: 0.6 parts; Nickel dibutyldithiocarbamate: 0.5 parts;
[0030] (2) Mix chlorosulfonated polyethylene Haplon-40 for 3 minutes, then add magnesium oxide, yellow lead masterbatch, paraffin, polyethylene glycol, coumarone, antimony trioxide, and dioctyl phthalate Ester, semi-reinforcing carbon black, and talcum powder were mixed for 6 minutes to make the mixture evenly stirred; Then knead for another 30 seconds; then move the mixed material to the mill for sheeting to dissipate heat. T...
Embodiment 3
[0039] The manufacturing steps of sheath rubber are as follows:
[0040] (1) Prepare raw materials according to the following components and weight content: chlorosulfonated polyethylene Haplon-40: 20 parts; Magnesium oxide: 1.2 parts; Huangdan masterbatch: 4.0 parts; Paraffin wax: 0.8 parts; Polyethylene glycol: 0.8 coumarone: 0.7 parts; antimony trioxide: 1.8 parts; dioctyl phthalate: 2.8 parts; semi-reinforcing carbon black: 6.0 parts; talcum powder: 5.2 parts; Lamb: 0.4 parts; Dibenzothiazole disulfide: 0.5 parts; Nickel dibutyldithiocarbamate: 0.3 parts;
[0041] (2) First mix chlorosulfonated polyethylene Haplon-40 for 3 minutes, then add magnesium oxide, yellow lead masterbatch, paraffin, polyethylene glycol, coumadin, antimony trioxide, and dioctyl phthalate Ester, semi-reinforcing carbon black, and talcum powder were mixed for 6 minutes to make the mixture evenly stirred; Then knead for another 30 seconds; then move the mixed material to the mill for sheeting to dis...
PUM
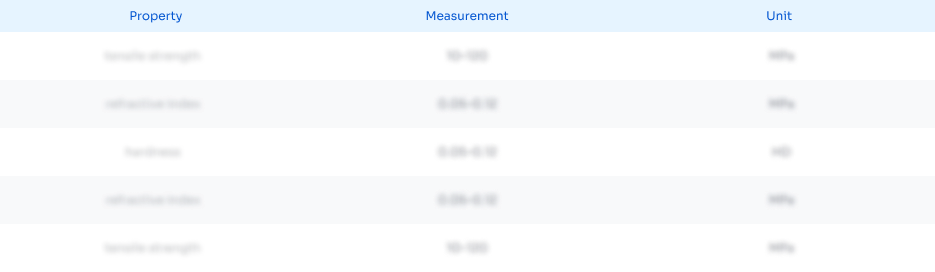
Abstract
Description
Claims
Application Information

- R&D
- Intellectual Property
- Life Sciences
- Materials
- Tech Scout
- Unparalleled Data Quality
- Higher Quality Content
- 60% Fewer Hallucinations
Browse by: Latest US Patents, China's latest patents, Technical Efficacy Thesaurus, Application Domain, Technology Topic, Popular Technical Reports.
© 2025 PatSnap. All rights reserved.Legal|Privacy policy|Modern Slavery Act Transparency Statement|Sitemap|About US| Contact US: help@patsnap.com