Core mold for spinning and forming large-size complex curved generatrix thin-wall member with transverse inner ribs
A thin-walled component, spinning forming technology, applied in forming tools, metal processing equipment, manufacturing tools, etc., can solve the problems of scratches on the inner wall of the workpiece, damage and scrap, waste of human, material and financial resources, etc., to achieve low manufacturing costs, easy to machine Processed, easy-to-assemble effects
- Summary
- Abstract
- Description
- Claims
- Application Information
AI Technical Summary
Problems solved by technology
Method used
Image
Examples
Embodiment Construction
[0024] This embodiment is a horizontal and vertical combined split mold used in the spinning forming of a large complex curved generatrix thin-walled component with horizontal inner ribs. Including mandrel head 1, splint 2 and mandrel tail 3, such as figure 1 As shown, and the mandrel head 1, splint 2 and mandrel tail 3 are all rotary bodies. Among them, the splint 2 is located between the mandrel head 1 and the mandrel tail 3, and is set on the positioning shaft of the mandrel tail 3; the splint 2 and the mandrel head 1 are hollow shells, and the splint 2 and the core The profiles of the die head 1 are all curved generatrix type. The inner hole of the mandrel head 1 is a stepped hole; the diameter of the inner hole at one end of the mandrel head 1 is the same as the outer diameter of the positioning shaft on the mandrel tail 3, forming an assembly hole for the mandrel tail positioning shaft; On the end face of part 1, there is a groove in the assembly hole of the positionin...
PUM
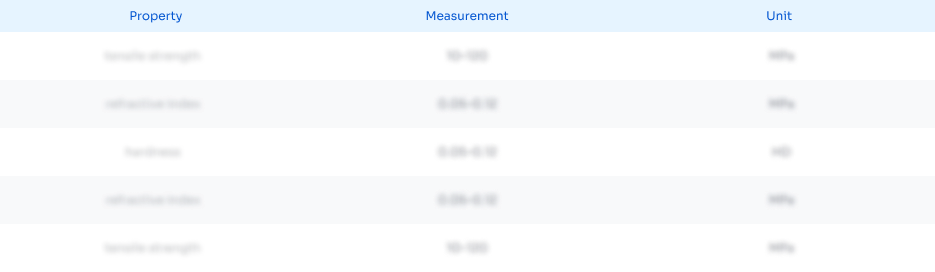
Abstract
Description
Claims
Application Information

- R&D
- Intellectual Property
- Life Sciences
- Materials
- Tech Scout
- Unparalleled Data Quality
- Higher Quality Content
- 60% Fewer Hallucinations
Browse by: Latest US Patents, China's latest patents, Technical Efficacy Thesaurus, Application Domain, Technology Topic, Popular Technical Reports.
© 2025 PatSnap. All rights reserved.Legal|Privacy policy|Modern Slavery Act Transparency Statement|Sitemap|About US| Contact US: help@patsnap.com