Method for preparing anti-polluting oil-water separation ultra-filtration membrane
A technology of oil-water separation and ultrafiltration membrane, which is applied in semi-permeable membrane separation, chemical instruments and methods, permeation/dialysis water/sewage treatment, etc. It can solve the problems of fast attenuation of oil droplets and achieve excellent anti-oil pollution performance, simple preparation process and high oil droplet retention rate.
- Summary
- Abstract
- Description
- Claims
- Application Information
AI Technical Summary
Problems solved by technology
Method used
Image
Examples
Embodiment 1
[0015] Weigh 3.2g of CA and 10.8g of solvent N, N-dimethylformamide into a three-necked flask, put it in a 60°C water bath at 900r / min and stir to dissolve for 1h, then weigh 6.0g of ethyl orthosilicate, Stir at 60°C for 5 hours to obtain a transparent and clear homogeneous casting solution; after stirring evenly, let the casting solution stand at 60°C for 5-7 hours to remove the bubbles in the casting solution; take a clean ordinary glass plate, homemade Put the scraper flat on the table. After scrubbing with absolute ethanol, take out the casting solution from the constant temperature bath. After the casting solution is completely cooled to room temperature, cast the casting solution on one end of the glass plate, and pull the scraper at a constant speed. To the other end of the glass plate, scrape out a nascent film with a thickness of about 240 μm on the glass plate; after scraping the nascent film, place it in the air for 10-30 seconds and then immerse it in a gel bath at ...
Embodiment 2
[0018] Weigh 3.2g of CA and 10.8g of solvent N, N-dimethylformamide into a three-necked flask, put it in a 60°C water bath at 900r / min and stir to dissolve for 1h, then weigh 6.0g of ethyl orthosilicate, Stir at 60°C for 5 hours to obtain a transparent and clear homogeneous casting solution; after stirring evenly, let the casting solution stand at 60°C for 5-7 hours to remove the bubbles in the casting solution; take a clean ordinary glass plate, homemade Put the scraper flat on the table. After scrubbing with absolute ethanol, take out the casting solution from the constant temperature bath. After the casting solution is completely cooled to room temperature, cast the casting solution on one end of the glass plate, and pull the scraper at a constant speed. To the other end of the glass plate, scrape out a nascent film with a thickness of about 240 μm on the glass plate; after scraping the nascent film, place it in the air for 10-30 seconds and then immerse it in a gel bath at ...
Embodiment 3
[0021] Weigh 3.2g of CA and 12.8g of solvent N, N-dimethylformamide into a three-necked flask, put it in a 60°C water bath at 900r / min and stir to dissolve for 1h, then weigh 4.0g of ethyl orthosilicate, Stir at 60°C for 5 hours to obtain a transparent and clear homogeneous casting solution; after stirring evenly, let the casting solution stand at 60°C for 5-7 hours to remove the bubbles in the casting solution; take a clean ordinary glass plate, homemade Put the scraper flat on the table. After scrubbing with absolute ethanol, take out the casting solution from the constant temperature bath. After the casting solution is completely cooled to room temperature, cast the casting solution on one end of the glass plate, and pull the scraper at a constant speed. To the other end of the glass plate, scrape out a nascent film with a thickness of about 240 μm on the glass plate; after scraping the nascent film, place it in the air for 10-30 seconds and then immerse it in a gel bath at ...
PUM
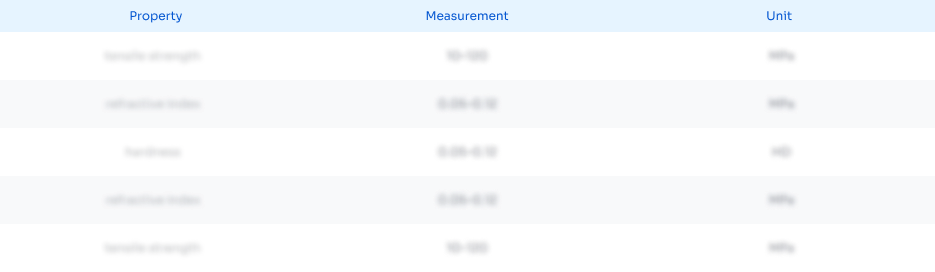
Abstract
Description
Claims
Application Information

- R&D
- Intellectual Property
- Life Sciences
- Materials
- Tech Scout
- Unparalleled Data Quality
- Higher Quality Content
- 60% Fewer Hallucinations
Browse by: Latest US Patents, China's latest patents, Technical Efficacy Thesaurus, Application Domain, Technology Topic, Popular Technical Reports.
© 2025 PatSnap. All rights reserved.Legal|Privacy policy|Modern Slavery Act Transparency Statement|Sitemap|About US| Contact US: help@patsnap.com