Composite casting method of aluminum cooling plate
A composite casting and cooling plate technology, applied in cooling/ventilation/heating transformation, electrical components, electrical solid devices, etc., can solve the problems of high production cost, low production efficiency, and large material consumption, so as to improve quality and production Efficiency, the effect of reducing production costs
- Summary
- Abstract
- Description
- Claims
- Application Information
AI Technical Summary
Problems solved by technology
Method used
Image
Examples
example 1
[0036] The selected aluminum tube grade is 1060 industrial pure aluminum, and its composition (weight percentage) is Si: 0.15%, Fe: 0.18%, Cu: 0.02%, Zn: 0.02%, Mn: 0.01%, Mg: 0.01%, and the rest is Al. The cross section of the aluminum tube is circular, the outer diameter is 8mm, and the wall thickness is 1mm. The base material of the aluminum cooling plate is ZL305 aluminum alloy for industrial use, and its composition is (percentage by weight) Mg: 8.20%, Zn: 1.21%, Ti: 0.15%, Fe: 0.2%, Si: 0.15%, Ni: 0.05%, Mn : 0.01%, Cu: 0.01%, and the rest is Al. The liquidus line of ZL305 alloy is 610°C.
[0037] The specific process is as follows:
[0038] 1) Aluminum tube preparation and forming
[0039] Bending the 1060 aluminum tube on the master form according to the required shape. When bending, the bending radius is required to be greater than 2 times the diameter of the aluminum tube to reduce wrinkling or cracking of the aluminum tube. After the bending is completed, poli...
example 2
[0046] The selected aluminum tube grade is 6061, and its composition (weight percentage) is Mg: 1.1%, Si: 0.62%, Fe: 0.65%, Cu: 0.29%, Mn: 0.13%, Zn: 0.22%, Cr: 0.10% , Ti: 0.15%, the rest is Al. The cross-section of the aluminum tube is circular, with an outer diameter of 6 mm and a wall thickness of 1 mm. The base material of the aluminum cooling plate is ZL101A aluminum alloy for industrial use, and its composition is (weight percent): Si: 6.93%, Mg: 0.38%, Ti: 0.15%, Fe: 0.17%, Ni: 0.05%, Zn: 0.01%, Cu : 0.01%, Mn: 0.01%, Sn: 0.01%, and the rest is Al. The liquidus and solidus temperatures of the ZL101A alloy are 615°C and 560°C, respectively.
[0047] The specific process is as follows:
[0048] 1) Aluminum tube preparation and forming
[0049] The aluminum tube is preheated to 100°C in a resistance furnace, and the wood alloy (its composition weight percentage is Bi: 50%, Pb: 25%, Sn: 12.5%, Cd: 12.5%) is melted in a water bath at 100°C Finally, the Wood alloy is po...
PUM
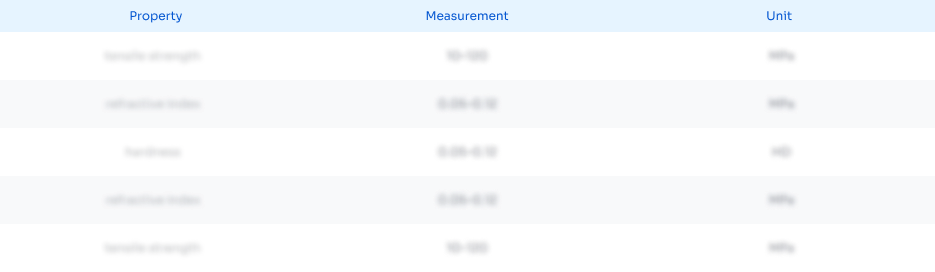
Abstract
Description
Claims
Application Information

- Generate Ideas
- Intellectual Property
- Life Sciences
- Materials
- Tech Scout
- Unparalleled Data Quality
- Higher Quality Content
- 60% Fewer Hallucinations
Browse by: Latest US Patents, China's latest patents, Technical Efficacy Thesaurus, Application Domain, Technology Topic, Popular Technical Reports.
© 2025 PatSnap. All rights reserved.Legal|Privacy policy|Modern Slavery Act Transparency Statement|Sitemap|About US| Contact US: help@patsnap.com