Hearth temperature area airflow heat insulation device for mesh belt-free silicon battery plate sintering furnace
A technology of silicon cells and heat insulation devices, applied in the direction of electrical components, furnaces, circuits, etc., can solve the problems of energy waste, large floor space, and large power consumption, so as to reduce production costs, reduce heat consumption, and improve The effect of sintering efficiency
- Summary
- Abstract
- Description
- Claims
- Application Information
AI Technical Summary
Problems solved by technology
Method used
Image
Examples
Embodiment Construction
[0014] The air flow heat insulation device in the furnace temperature zone of the non-mesh belt silicon cell sintering furnace, figure 1 , figure 2 , image 3 As shown, it includes a preheating debinding area 21, a heating area 22, a sintering area 23 and a cooling area 24, and is separated by a heat insulating board 25 between each area. Air flow cut-off door 8 is all provided with between cooling zone 24, and is close to insulation plate 25, and air flow cut-off door 8 is made of jet pipe 81, suction pipe 82, intake pipe 83, suction pipe 84, air flow chamber 85 and circulation Pump 86 is made up of, jet pipe 81 and suction pipe 82 are all perpendicular to the direction of the tunnel and correspondingly arranged, and all jet pipes 81 are connected with intake pipe 83, and all suction pipes 82 are connected with suction pipe 84, and intake pipe 83, suction pipe Trachea 84 links to each other with airflow chamber 85, and circulation pump 86 is arranged on the outlet of airfl...
PUM
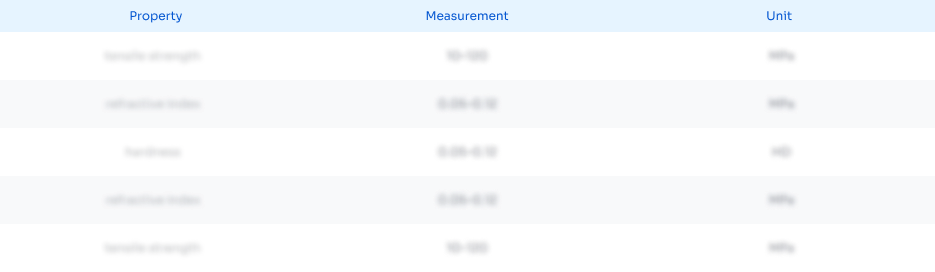
Abstract
Description
Claims
Application Information

- R&D Engineer
- R&D Manager
- IP Professional
- Industry Leading Data Capabilities
- Powerful AI technology
- Patent DNA Extraction
Browse by: Latest US Patents, China's latest patents, Technical Efficacy Thesaurus, Application Domain, Technology Topic, Popular Technical Reports.
© 2024 PatSnap. All rights reserved.Legal|Privacy policy|Modern Slavery Act Transparency Statement|Sitemap|About US| Contact US: help@patsnap.com