Method for extracting krill oil with high phosphatide content from Antarctic krills
A technology of Antarctic krill oil and Antarctic krill, applied in the direction of fat oil/fat production, fat production, etc., can solve the problems of high extraction process temperature, large difference between Antarctic krill and lobster components, and inability to extract Antarctic krill shrimp oil, etc. , to achieve high extraction efficiency and good phospholipid enrichment effect
- Summary
- Abstract
- Description
- Claims
- Application Information
AI Technical Summary
Problems solved by technology
Method used
Examples
Embodiment 1
[0013] (1) drying: drying fresh Antarctic krill at 55-75°C to obtain dry Antarctic krill with a water content (mass percentage) of 8-10%;
[0014] (2) Extraction: Take n-hexane 6.5 times the weight of dried Antarctic krill and extract the dried Antarctic krill for 3 times at 25-30°C, and filter out the dried Antarctic krill for each extraction; after 3 extractions , the extraction rate of phospholipids was 92.0%;
[0015] (3) Solvent volatilization: combine the extracts for 3 times, evaporate the extracts at a temperature of 25~55°C and a vacuum of -0.06~-0.085Mpa, remove the n-hexane in the extracts, and obtain the phospholipid content (mass percentage ) is 32.0% Antarctic krill oil; then nitrogen or carbon dioxide gas is continuously passed through the Antarctic krill oil at normal temperature to remove residual n-hexane in the shrimp oil, so that the residual amount of n-hexane meets the national standard;
[0016] (4) Enrichment of phospholipids: adding the concentration ...
Embodiment 2
[0018] (1) drying: drying fresh Antarctic krill at 55-75°C to obtain dry Antarctic krill with a water content (mass percentage) of 8-10%;
[0019] (2) Extraction: Take No. 6 gasoline that is 6 times the weight of dried Antarctic krill and extract dried Antarctic krill for 4 times at 25-35°C. For each extraction, filter out the dried Antarctic krill; after 4 extractions After that, the extraction rate of phospholipids was 92.2%;
[0020] (3) Solvent volatilization: merging the extracts for 4 times, evaporating the extracts at a temperature of 25~55°C and a vacuum of -0.06~-0.085Mpa, removing No. 6 gasoline in the extracts to obtain the phospholipid content (mass percent content) is 31.5% of the Antarctic krill oil; then the Antarctic krill oil is continuously fed with nitrogen or carbon dioxide gas at room temperature to remove the residual No. 6 gasoline in the shrimp oil, so that the residual amount meets the national standard;
[0021] (4) Enrichment of phospholipids: addin...
Embodiment 3
[0023] (1) drying: drying fresh Antarctic krill at 55-75°C to obtain dry Antarctic krill with a water content (mass percentage) of 8-10%;
[0024] (2) Extraction: Take petroleum ether 7 times the weight of dried Antarctic krill and extract the dried Antarctic krill for 3 times at 25-35°C, and use filter paper to filter out the dried Antarctic krill for each extraction; after 3 extractions , the extraction rate of phospholipids is 91.5%;
[0025] (3) Solvent volatilization: Combine the extracts for 3 times, evaporate the extracts at a temperature of 25 to 55°C and a vacuum of -0.06 to -0.085Mpa, remove the petroleum ether in the extracts, and obtain a mass percentage of phospholipids of 31.5 % of the Antarctic krill oil; then the Antarctic krill oil is continuously fed with nitrogen or carbon dioxide gas at normal temperature to remove the residual petroleum ether in the shrimp oil, so that the residual petroleum ether meets the national standard;
[0026] (4) Enrichment of ph...
PUM
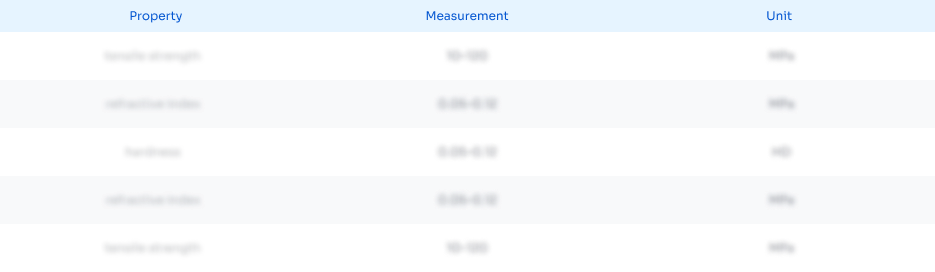
Abstract
Description
Claims
Application Information

- R&D
- Intellectual Property
- Life Sciences
- Materials
- Tech Scout
- Unparalleled Data Quality
- Higher Quality Content
- 60% Fewer Hallucinations
Browse by: Latest US Patents, China's latest patents, Technical Efficacy Thesaurus, Application Domain, Technology Topic, Popular Technical Reports.
© 2025 PatSnap. All rights reserved.Legal|Privacy policy|Modern Slavery Act Transparency Statement|Sitemap|About US| Contact US: help@patsnap.com