Method for widening catalytic reforming feedstock
A catalytic reforming and raw material technology, which is applied in the petroleum industry, hydroprocessing process, and hydrocarbon oil treatment, can solve the problems of unqualified nitrogen content in refined oil, affecting the processing capacity of the device, and unqualified sulfur content in products, etc. source, reduce pressure drop, and prevent channeling
- Summary
- Abstract
- Description
- Claims
- Application Information
AI Technical Summary
Problems solved by technology
Method used
Image
Examples
Embodiment 1
[0039] A kind of FCC stabilized gasoline and a kind of straight-run naphtha are used as raw materials, and their properties are shown in Table 2. FCC stabilized gasoline and straight-run naphtha were mixed at a ratio of 20:80 (wt%) to obtain mixed naphtha A, whose properties are shown in Table 2. Mixed naphtha C is contacted with hydrogenation catalyst DN3110 in the reactor for hydrogenation reaction. Two reactors are used, the catalyst loading ratio is 50:50, and no quenching hydrogen is injected between the reactors. The reaction conditions are: reaction pressure 2.5MPa(g), first reactor inlet temperature 280°C, volume space velocity (LHSV) 2.5h -1 , hydrogen oil volume ratio 250Nm 3 / m 3 . The reaction product is stripped and fractionated to obtain refined naphtha. The operating conditions and product properties are shown in Table 3.
[0040] It can be seen from Table 3 that when blending low-proportion FCC-stabilized gasoline, due to the low olefin content, the temper...
Embodiment 2
[0042] The same FCC stable gasoline in Example 1 is mixed with straight-run naphtha at 50:50 (wt%) to obtain mixed naphtha B, whose properties are shown in Table 2. Mixed naphtha B was contacted with hydrogenation catalyst DN3110 in a reactor for hydrogenation reaction. The reaction conditions were the same as in Example 1, and the operating conditions and product properties were shown in Table 3.
[0043] It can be seen from Table 3 that when the proportion of blended FCC stable gasoline reaches 50wt%, the content of sulfur, nitrogen and olefins in the mixed oil is relatively high, the nitrogen content reaches 27μg / g, and the bromine value is 28gBr / 100g. Under the existing reaction conditions, the partial pressure of hydrogen can no longer meet the requirements of denitrification, and the nitrogen content of hydrogenation products exceeds the standard. At the same time, the content of olefins in the raw oil is high, and the temperature rise of the pre-hydrogenation reactor be...
Embodiment 3
[0045] The same mixed naphtha B in Example 2 was contacted with hydrogenation catalyst DN3110 in the reactor for hydrogenation reaction, the catalyst loading ratio was 40:60, and quenched hydrogen was injected between the reactors. The reaction conditions are: reaction pressure 3.6MPa(g), first reactor inlet temperature 280°C, volume space velocity (LHSV) 2.6h -1 , hydrogen oil volume ratio 300Nm 3 / m 3 . The operating conditions and product properties are shown in Table 3.
[0046] It can be seen from Table 3 that when the reaction pressure is increased to 3.6MPa(g), the catalyst loading ratio is 40:60 and cold hydrogen is injected, the sulfur and nitrogen content of the hydrogenation product meets the requirements of the reforming feed, and the secondary reaction outlet The temperature is only 319°C, and the content of impurities such as sulfur and nitrogen in the hydrogenation product meets the requirements of the reforming feed.
PUM
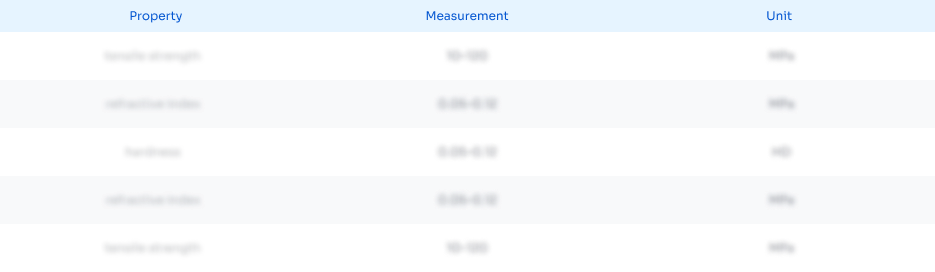
Abstract
Description
Claims
Application Information

- R&D
- Intellectual Property
- Life Sciences
- Materials
- Tech Scout
- Unparalleled Data Quality
- Higher Quality Content
- 60% Fewer Hallucinations
Browse by: Latest US Patents, China's latest patents, Technical Efficacy Thesaurus, Application Domain, Technology Topic, Popular Technical Reports.
© 2025 PatSnap. All rights reserved.Legal|Privacy policy|Modern Slavery Act Transparency Statement|Sitemap|About US| Contact US: help@patsnap.com