Method for manufacturing refined high cleanliness Al-Ti-B alloy
A technology with high cleanliness and manufacturing method, which is applied in the field of manufacturing technology of aluminum-titanium-boron alloy materials, can solve the problems that cannot meet the requirements of aluminum alloy material refinement treatment, etc., and achieve the goal of reducing impurities, improving cleanliness, and high cleanliness Effect
- Summary
- Abstract
- Description
- Claims
- Application Information
AI Technical Summary
Problems solved by technology
Method used
Examples
Embodiment 1
[0017] Example 1: Manufacture of high clean aluminum titanium boron wire (AlTi5B1)
[0018] The aluminum-titanium-boron refining agent containing 5% titanium and 1% boron is the most widely used refining material for deformed aluminum alloys, especially aluminum alloy profiles, plates, strips, etc.
[0019] Add 1050kg of 99.7% aluminum ingot to medium-frequency induction aluminum to melt, and heat to 720°C, add 230kg of potassium fluotitanate with a purity of 98% and 120kg of fluoroboric acid with a purity of 98% under the action of medium-frequency electromagnetic force (frequency 1000 Hz) The potassium mixture is placed on the surface of the molten aluminum and the temperature of the molten aluminum is maintained. Continue medium-frequency electromagnetic stirring and heat preservation for 30 minutes. After the reaction is completed, after the sampling components are qualified (titanium content 4.5-5.5%, boron content 0.8-1.2%), pour out the reaction by-products floating on ...
Embodiment 2
[0020] Example 2: Manufacture of High Clean AlTi5B0.2 AlTi5B0.2 Alloy
[0021] The Al-Ti-B refining agent containing 5% titanium and 0.2% boron is a kind of refining treatment material widely used in aluminum alloy profiles, especially aluminum alloy profiles that use part of the recycled materials as raw materials.
[0022]Add 1050kg of 99.7% aluminum ingot to medium frequency induction aluminum to melt, and heat to 700-740°C, add 230kg of potassium fluotitanate with a purity of 98% and 25kg of potassium fluotitanate with a purity of 98% under the action of medium frequency electromagnetic force (frequency 1000 Hz) Potassium fluoroborate is mixed on the surface of molten aluminum, and the temperature of molten aluminum is maintained. Continue medium-frequency electromagnetic stirring and heat preservation for 30 minutes. After the reaction is completed, after the sampling components are qualified (titanium content 4.5-5.5%, boron content 0.18-0.24%), pour out the reaction by...
PUM
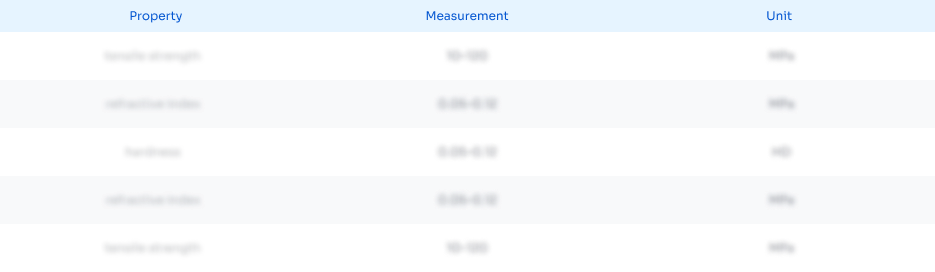
Abstract
Description
Claims
Application Information

- Generate Ideas
- Intellectual Property
- Life Sciences
- Materials
- Tech Scout
- Unparalleled Data Quality
- Higher Quality Content
- 60% Fewer Hallucinations
Browse by: Latest US Patents, China's latest patents, Technical Efficacy Thesaurus, Application Domain, Technology Topic, Popular Technical Reports.
© 2025 PatSnap. All rights reserved.Legal|Privacy policy|Modern Slavery Act Transparency Statement|Sitemap|About US| Contact US: help@patsnap.com