Production process of coarse particle nickel acetate
A production process, technology of nickel acetate, applied in the separation/purification of carboxylic acid compounds, preparation of carboxylate, organic chemistry, etc., can solve the problem of easy agglomeration of powdered nickel acetate, insufficient lump content, affecting product solubility, etc. problems, to achieve the effects of high production efficiency, quality improvement, and high one-time recovery rate
- Summary
- Abstract
- Description
- Claims
- Application Information
AI Technical Summary
Problems solved by technology
Method used
Image
Examples
Embodiment 1
[0017] Embodiment 1: the production process of superfine powder grade nickel acetate is described as follows:
[0018] 1. Synthesis: first add a certain amount of glacial acetic acid (content above 99.5%, industrial grade) into the synthesis reaction kettle, and then add basic nickel carbonate (Ni content 19%±1%) to control basic nickel carbonate: ice Acetic acid=1︰1.1~1.5 (molar ratio), the stirring rate is 80~85r / min, according to the reaction situation, add glacial acetic acid and basic nickel carbonate in batches, and continue the reaction until the reaction is complete, pay attention to control the reaction temperature not to exceed 40°C . Whether the reaction is complete can be judged by monitoring the pH value of the final reaction solution. The pH should be controlled at 4.0±0.1. If the pH value is too high, nickel acetate will be easily emulsified. If the pH value is too low, the product will not be easy to dry evenly.
[0019] 2. Dehydration: The synthesized nickel...
Embodiment 2
[0022] The selected raw materials are glacial acetic acid (content 99.6%, industrial grade), basic nickel carbonate (Ni content 19%), basic nickel carbonate: glacial acetic acid = 1: 1.4 (molar ratio), stirring speed 80-85r / min, Process and other process parameters are the same as in Example 1.
Embodiment 3
[0024] The selected raw materials are glacial acetic acid (content 99.8%, industrial grade), basic nickel carbonate (Ni content 20%), basic nickel carbonate: glacial acetic acid = 1: 1.3 (molar ratio), stirring speed 80-85r / min, The reaction temperature is 30-40° C., and the process and other process parameters are the same as in Example 1.
PUM
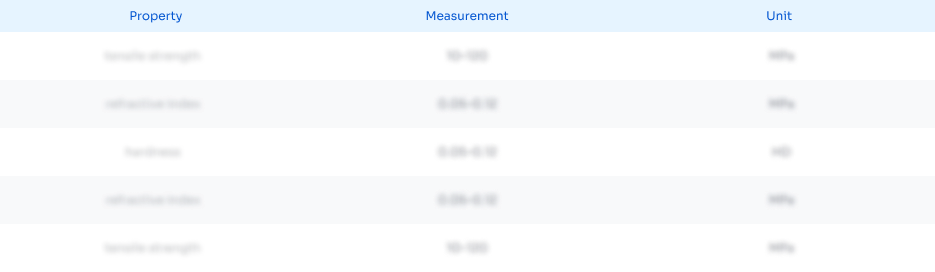
Abstract
Description
Claims
Application Information

- R&D Engineer
- R&D Manager
- IP Professional
- Industry Leading Data Capabilities
- Powerful AI technology
- Patent DNA Extraction
Browse by: Latest US Patents, China's latest patents, Technical Efficacy Thesaurus, Application Domain, Technology Topic, Popular Technical Reports.
© 2024 PatSnap. All rights reserved.Legal|Privacy policy|Modern Slavery Act Transparency Statement|Sitemap|About US| Contact US: help@patsnap.com