Tooth punching die for saw blade substrate
A technology of matrix and punching teeth, which is applied in the cutting tool manufacturing, forming tools, manufacturing tools and other directions of sawing machine devices to achieve the effect of improving tooth indexing, ensuring completeness and improving tooth profile processing efficiency.
- Summary
- Abstract
- Description
- Claims
- Application Information
AI Technical Summary
Problems solved by technology
Method used
Image
Examples
Embodiment Construction
[0016] like figure 1 , figure 2 and image 3 As shown, a saw blade matrix stamping die includes an upper mold frame 7 and a lower mold frame 6, the die 1 is fixed on the lower mold frame 6 through the die fixing plate 3, and the punch 2 is fixed on the lower mold frame 6 through the punch fixing plate 4. On the upper mold frame 7, the unloading device 5 is fixed on the punch fixed plate 4, the punch 2 and the die 1 are provided with rough punching teeth 11 and fine punching teeth 12, and the size of the rough punching teeth 11 is smaller than the fine punching teeth 12.
[0017] The engineering process of the present invention is as follows: first the saw blade base body 9 is fixed on the indexing device 10, the distance between the saw blade base body 9 and the die 1 is adjusted, the pneumatic punch press 8 punches the teeth, and after the rough punching teeth 11 are punched, pass The indexing device rotates a tooth index, and the rough punching tooth 11 is smaller than th...
PUM
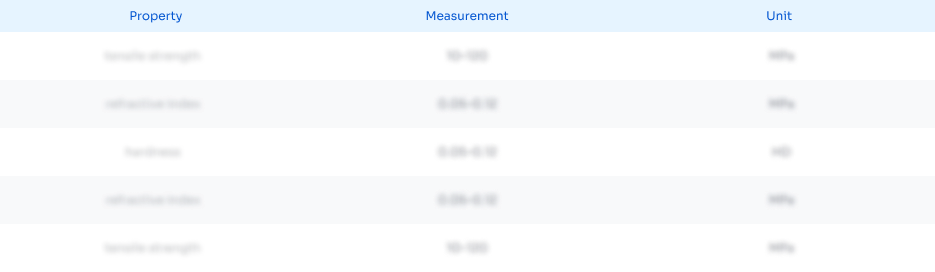
Abstract
Description
Claims
Application Information

- R&D Engineer
- R&D Manager
- IP Professional
- Industry Leading Data Capabilities
- Powerful AI technology
- Patent DNA Extraction
Browse by: Latest US Patents, China's latest patents, Technical Efficacy Thesaurus, Application Domain, Technology Topic, Popular Technical Reports.
© 2024 PatSnap. All rights reserved.Legal|Privacy policy|Modern Slavery Act Transparency Statement|Sitemap|About US| Contact US: help@patsnap.com