Rare earth Er microalloyed Al-Zn-Mg-Cu alloy and preparation method thereof
A technology of microalloying and alloying, applied in the field of metal alloys, can solve the problem of no report on microalloying
- Summary
- Abstract
- Description
- Claims
- Application Information
AI Technical Summary
Problems solved by technology
Method used
Image
Examples
example 1
[0021] Example 1: Using high-purity aluminum (Al99.70), high-purity Mg (Mg9995), industrial pure Zn (Zn≥98.7wt.%) and Al-5.03Cu, Al-6.00Er (except the alloy without adding Er) , Al-4.50Zr master alloy as the raw material, according to the chemical composition requirements of the alloy in Table 1. First put the aluminum ingot into the furnace, and after the aluminum ingot is melted, add pure zinc, aluminum-copper master alloy, aluminum-zirconium master alloy and aluminum-erbium master alloy successively. After the metal and the intermediate alloy are melted, remove the dross on the surface of the melt, and when the melt temperature reaches 715-735°C, add pure magnesium. In order to distribute the alloying elements evenly, stir the melt, and then refine it. Refining is placed at 710-730°C for 20-35 minutes, then the scum on the surface is removed, and then it is placed at a casting temperature of 700-720°C. Cast into alloy billets. Two-stage homogenization annealing is carried...
example 2
[0025] Example 2: Using high-purity aluminum (Al99.70), high-purity Mg (Mg9995), industrial pure Zn (Zn≥98.7wt.%) and Al-5.03Cu, Al-6.00Er (except the alloy without adding Er) , Al-4.50Zr master alloy as the raw material, according to the chemical composition requirements of the alloy in Table 1. First put the aluminum ingot into the furnace, and after the aluminum ingot is melted, add pure zinc, aluminum-copper master alloy, aluminum-zirconium master alloy and aluminum-erbium master alloy successively. After the metal and the intermediate alloy are melted, remove the dross on the surface of the melt, and when the melt temperature reaches 715-735°C, add pure magnesium. In order to distribute the alloying elements evenly, the melt is stirred. Refining is carried out afterwards, and the refining is left to stand at 710-730°C for 20-35 minutes, then the scum on the surface is removed, and then left to stand at a casting temperature of 700-720°C before being cast into an alloy in...
example 3
[0029] Example 3: Using high-purity aluminum (Al99.70), high-purity Mg (Mg9995), industrial pure Zn (Zn≥98.7wt.%) and Al-5.03Cu, Al-6.00Er (except the alloy without adding Er) , Al-4.50Zr master alloy as the raw material, according to the chemical composition requirements of the alloy in Table 1. First put the aluminum ingot into the furnace, and after the aluminum ingot is melted, add pure zinc, aluminum-copper master alloy, aluminum-zirconium master alloy and aluminum-erbium master alloy successively. After the metal and the intermediate alloy are melted, remove the dross on the surface of the melt, and when the melt temperature reaches 715-735°C, add pure magnesium. In order to distribute the alloying elements evenly, the melt is stirred. Refining is carried out afterwards, and the refining is left to stand at 710-730°C for 20-35 minutes, then the scum on the surface is removed, and then left to stand at a casting temperature of 700-720°C before being cast into an alloy in...
PUM
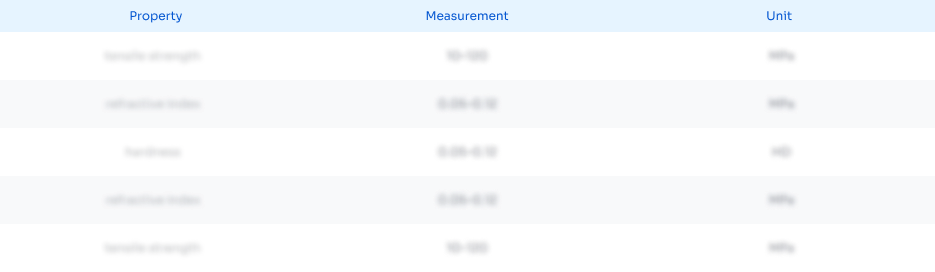
Abstract
Description
Claims
Application Information

- R&D
- Intellectual Property
- Life Sciences
- Materials
- Tech Scout
- Unparalleled Data Quality
- Higher Quality Content
- 60% Fewer Hallucinations
Browse by: Latest US Patents, China's latest patents, Technical Efficacy Thesaurus, Application Domain, Technology Topic, Popular Technical Reports.
© 2025 PatSnap. All rights reserved.Legal|Privacy policy|Modern Slavery Act Transparency Statement|Sitemap|About US| Contact US: help@patsnap.com