Compound preparation method of aluminum alloy and magnesium alloy laminated plate
An aluminum alloy and magnesium alloy technology, which is applied in metal processing equipment, welding equipment, manufacturing tools, etc., can solve the problems such as no reports of magnesium alloy and aluminum alloy explosive composite materials, and achieve simple and easy operation and mechanical properties of the explosive composite process. High, enhance the effect of damping and vibration reduction
- Summary
- Abstract
- Description
- Claims
- Application Information
AI Technical Summary
Problems solved by technology
Method used
Image
Examples
preparation example Construction
[0038] A composite preparation method of an aluminum alloy and a magnesium alloy laminate, comprising the following steps:
[0039] ①Substrate and doubler board preparation: The size of the doubler board should be larger than the base board. According to the overall size of the doubler board, leave a space of 20mm to 100mm around the doubler board. 5mm groove, and leveling treatment and surface grinding and cleaning of the base plate and double board; the aforementioned base plate and double board are aluminum alloy and magnesium alloy, or magnesium alloy and aluminum alloy;
[0040] ② Preheating treatment of base plate and double plate: heat the base plate and double plate to 120 ℃ ~ 200 ℃ before explosive compounding, and carry out heat preservation treatment;
[0041] ③ Explosive composite foundation: use clay or fine sand for compaction, and lay 3mm to 8mm fiber composite board on the surface as the explosive composite base;
[0042] ④ Explosive preparation: Ammonium nitr...
Embodiment 1
[0053] Example 1: Three-layer explosive composite material of 1A50 aluminum alloy plate, ZK60 magnesium alloy, and 1A50 aluminum alloy plate.
[0054] The substrate is a ZK60 magnesium alloy with a size of 20mm×500mm×1000mm, and the double board is a 1A50 aluminum alloy plate with a size of 5mm×550mm×1050mm. Use a grinding wheel to polish the substrate and doubler board to remove oxides on the metal surface, and open a semicircular groove of R2 on the doubler board corresponding to the edge of the substrate. The support distance between the doubler plate and the base plate is 3mm, the installation angle is 0°, the explosive is ammonium nitrate explosive with buffer added, and the charge is 5.5Kg; after the first explosive compounding, the 1A50 aluminum alloy-ZK60 magnesium alloy The composite plate is leveled. The 1A50 aluminum alloy-ZK60 magnesium alloy composite plate is used as the substrate, and the side of the ZK60 magnesium alloy is the explosive composite surface. Magn...
Embodiment 2
[0055] Example 2: 7A52 aluminum alloy, AZ31B magnesium alloy, and 7A52 aluminum alloy three-layer explosive composite board.
[0056] The substrate is AZ31B magnesium alloy with a size of 20mm×500mm×1000mm, and the double plate is 7A52 aluminum alloy with a size of 3mm×550mm×1050mm. 7A52 aluminum alloy is subjected to solid solution treatment before compounding. The process is 465°C×30min, and the transfer time of water quenching at room temperature is about 5s. Oxide, the doubler plate corresponds to the edge of the base plate to process R2 semicircular grooves, the support distance between the doubler plate and the base plate is 3mm, and the ammonium nitrate explosive with buffer is used, and the charge is 5Kg; after the first explosive compounding, the 7A52 aluminum The alloy-AZ31B magnesium alloy composite board is leveled. The 7A52 aluminum alloy-AZ31B magnesium alloy composite board is used as the substrate. The side of the AZ31B magnesium alloy is the explosive composit...
PUM
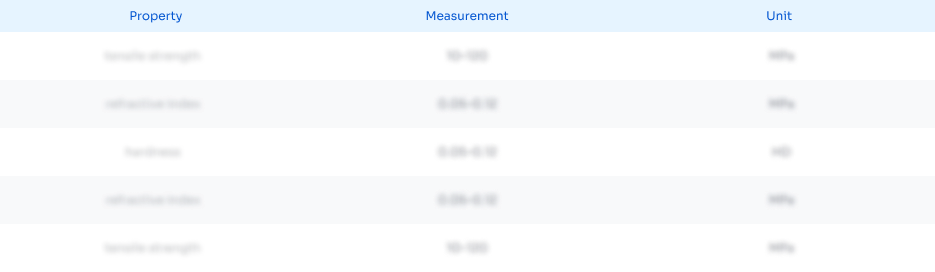
Abstract
Description
Claims
Application Information

- R&D
- Intellectual Property
- Life Sciences
- Materials
- Tech Scout
- Unparalleled Data Quality
- Higher Quality Content
- 60% Fewer Hallucinations
Browse by: Latest US Patents, China's latest patents, Technical Efficacy Thesaurus, Application Domain, Technology Topic, Popular Technical Reports.
© 2025 PatSnap. All rights reserved.Legal|Privacy policy|Modern Slavery Act Transparency Statement|Sitemap|About US| Contact US: help@patsnap.com