Method for preparing aluminum oxide nanofiber by electrostatic spinning
A nano- and electrospinning technology of alumina, which is applied in fiber processing, textile and papermaking, filament/wire forming, etc., can solve problems such as inability to guarantee the fiber formation and strength of alumina, poor experimental repeatability, and low aluminum content , to achieve the effects of enhanced strength, enhanced repeatability, and increased content
- Summary
- Abstract
- Description
- Claims
- Application Information
AI Technical Summary
Problems solved by technology
Method used
Examples
Embodiment 1
[0022] Weigh 0.83g of aluminum acetylacetonate, dissolve it in 15g of DMF, stir well to dissolve it completely; then weigh 1.67g of PAN, dissolve it in the above solution, and heat and stir at 50°C to make the whole system reach Uniform and transparent.
[0023] Then the obtained precursor solution was electrospun: the temperature was 20° C., the humidity was 50%, the output voltage was set to 18 KV, the propulsion speed of the propulsion pump was 30 μL / min, and the receiving distance was 12 cm. The resulting spun fibers were exposed to air for 24 hours to fully gel them.
[0024] Finally, the as-spun fibers obtained above were sintered under suitable conditions: the sintering atmosphere was air, the heating rate was 5°C / min, and the calcination temperature was 1400°C; ℃ for 1 hour, then cool down naturally.
[0025] After sintering, the alumina fiber maintains the fiber structure, and the diameter is greatly reduced. SEM results show that the continuity of the alumina fiber...
Embodiment 2
[0027] Weigh 1.67g of aluminum acetylacetonate, dissolve it in 15g of DMAc, stir well to dissolve it completely; then weigh 1.67g of PAN, dissolve it in the above solution, and heat and stir at 50°C to make the whole system reach Uniform and transparent.
[0028] Then the obtained precursor solution was subjected to electrospinning: the temperature was 25°C, the humidity was 42%, the output voltage was set to 18KV, the propulsion speed of the propulsion pump was 30 μL / min, and the receiving distance was 12cm. The resulting spun fibers were exposed to air for 24 hours to fully gel them.
[0029] Finally, the as-spun fibers obtained above were sintered under suitable conditions: the sintering atmosphere was air, the heating rate was 5°C / min, and the calcination temperature was 1400°C; ℃ for 1 hour, then cool down naturally.
[0030] After sintering, the alumina fiber still maintains the fiber structure well, and the diameter is greatly reduced. SEM results show that the contin...
Embodiment 3
[0032] Weigh 0.83g of aluminum acetylacetonate, dissolve it in 15g of DMF, stir well to dissolve it completely; then weigh 1.67g of PU, dissolve it in the above solution, and heat and stir at 70°C to make the whole system reach Uniform and transparent.
[0033] Then the obtained precursor solution was electrospun: the temperature was 27° C., the humidity was 56%, the output voltage was set to 18 KV, the propulsion speed of the propulsion pump was 20 μL / min, and the receiving distance was 15 cm. The resulting spun fibers were exposed to air for 24 hours to fully gel them.
[0034] Finally, the as-spun fibers obtained above were sintered under suitable conditions: the sintering atmosphere was air, the heating rate was 5°C / min, and the calcination temperature was 1300°C; ℃ for 1 hour, then cool down naturally.
[0035] After sintering, the alumina fiber still maintains the fiber structure well, and the diameter is greatly reduced. SEM results show that the continuity of the alu...
PUM
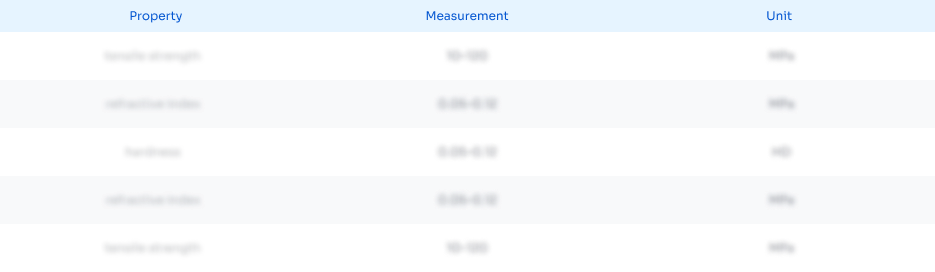
Abstract
Description
Claims
Application Information

- R&D Engineer
- R&D Manager
- IP Professional
- Industry Leading Data Capabilities
- Powerful AI technology
- Patent DNA Extraction
Browse by: Latest US Patents, China's latest patents, Technical Efficacy Thesaurus, Application Domain, Technology Topic, Popular Technical Reports.
© 2024 PatSnap. All rights reserved.Legal|Privacy policy|Modern Slavery Act Transparency Statement|Sitemap|About US| Contact US: help@patsnap.com