Optical fiber stripping solution and preparation method thereof, and optical fiber stripping method
A stripping liquid and optical fiber technology, applied in light guides, optics, optical components, etc., can solve the problems of slow speed, labor occupation, easy tearing, etc., and achieve the effect of increasing speed, saving labor, and avoiding breakage or damage
- Summary
- Abstract
- Description
- Claims
- Application Information
AI Technical Summary
Problems solved by technology
Method used
Image
Examples
Embodiment 1
[0033] (1) Take 0.3g of paraffin (melting point 60-70°C), heat to 115°C to melt; add 30ml of chloroform while stirring while hot;
[0034] (2) Add 3ml of 75wt% formic acid, 2g of benzoic acid and 2.5ml of acetophenone and mix well;
[0035] (3) Add 0.3 g of ethyl cellulose as a thickener, continue stirring and mixing to obtain the optical fiber stripping solution.
[0036] The optical fiber stripping method is: heat the optical fiber stripping solution to 45°C, soak the ribbon-shaped optical fiber to be stripped in it for 3 seconds, wait for 3 seconds to fully react after taking it out, then wipe the optical fiber clean with a paper towel, and remove the encapsulation layer . Optical fiber stripping condition: complete stripping; no damage to the core, cladding and coating.
Embodiment 2
[0038] (1) Take 0.4g of paraffin (melting point 75-90°C), heat to 145°C and melt; add 45ml of chloroform while stirring while hot;
[0039] (2) Add 5ml of 70wt% formic acid, 3.5g of benzoic acid and 4.5ml of acetophenone and mix well;
[0040] (3) Add 0.4 g of ethyl cellulose as a thickener, continue stirring and mixing to obtain an optical fiber stripping solution.
[0041] The optical fiber stripping method is: heat the optical fiber stripping solution to 45°C, soak the ribbon-shaped optical fiber to be stripped in it for 4 seconds, wait for 2.7 seconds to fully react after taking it out, and then wipe the optical fiber with a paper towel to remove the encapsulation layer . Optical fiber stripping condition: complete stripping; no damage to the core, cladding and coating.
Embodiment 3
[0043] (1) Take 0.5g of paraffin (melting point 70-80°C), heat to 125°C and melt; add 60ml of chloroform while stirring while hot;
[0044] (2) Add 8ml of 80wt% formic acid, 5g of benzoic acid and 6ml of acetophenone and mix well;
[0045] (3) Add 0.5g of ethyl cellulose as a thickener, continue stirring and mixing to obtain the optical fiber stripping solution.
[0046] The optical fiber stripping method is: heat the optical fiber stripping solution to 42°C, soak the ribbon-shaped optical fiber to be stripped in it for 4 seconds, wait for 2 seconds to fully react after taking it out, and then wipe the optical fiber with a paper towel to remove the encapsulation layer . Optical fiber stripping condition: complete stripping; no damage to the core, cladding and coating.
PUM
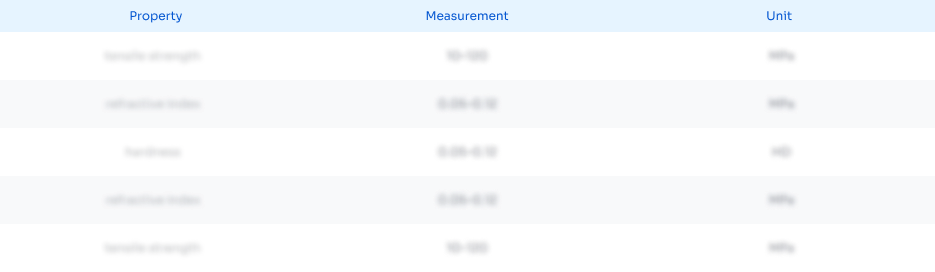
Abstract
Description
Claims
Application Information

- Generate Ideas
- Intellectual Property
- Life Sciences
- Materials
- Tech Scout
- Unparalleled Data Quality
- Higher Quality Content
- 60% Fewer Hallucinations
Browse by: Latest US Patents, China's latest patents, Technical Efficacy Thesaurus, Application Domain, Technology Topic, Popular Technical Reports.
© 2025 PatSnap. All rights reserved.Legal|Privacy policy|Modern Slavery Act Transparency Statement|Sitemap|About US| Contact US: help@patsnap.com