Method for recycling secondary lead by electrolyzing alkaline leaded solution
A technology for regenerating lead and solution, applied in the field of hydrometallurgy, can solve the problems of high DC power consumption, high acid electrolytic corrosion, unacceptable to manufacturers, etc., to reduce energy consumption, avoid secondary pollution, and achieve continuous and fully enclosed industrial production. Effect
- Summary
- Abstract
- Description
- Claims
- Application Information
AI Technical Summary
Problems solved by technology
Method used
Image
Examples
Embodiment 1
[0117] Take 10 pieces of 12V, 12Ah waste lead-acid batteries for electric vehicles purchased on the market. The total weight of the battery pack is 45.5 kg. The specific implementation process is as follows:
[0118] 1) After discharging the 10 batteries, they are put into a crusher to be broken, and the water phase is separated by density difference to obtain lead paste, grids, waste sulfuric acid, separators and shells.
[0119] 2) Put the pressure-filtered lead paste into a crusher and a ball mill in turn for smashing, and then use a 60-mesh stainless steel screen for sieving. The larger lead paste particles continue to be transferred to the crusher for crushing until all the lead paste is Through the screen.
[0120] 3) Take 40L of waste sulfuric acid obtained in the process of (1), after supplementing a small amount of concentrated sulfuric acid, adjust it to contain 5mol / L H 2 SO 4 , 0.5mol / L Fe(ClO 4 ) 2 And 0.5mol / L HClO 4 . Take 26 kilograms of lead paste powder and waste ...
Embodiment 2
[0127] Take a 12V, 54Ah lead-acid battery from a used automobile. The total weight of the battery pack is 15.5 kg. The specific recycling process is as follows:
[0128] According to the procedures (1) and (2) of Example 1, the lead paste, grids, spacers and plastics were separated.
[0129] 3) Take 12L of waste sulfuric acid obtained in the above process and adjust its acidity to a mixed solution containing 4.0mol / L sulfuric acid, 1mol / L ferrous perchlorate and 1mol / L perchloric acid. Take 6 kg of lead paste powder and waste sulfuric acid solution obtained by screening in (2), mix the two, and add 4.0mol / L sulfuric acid, 0.8mol / L ferrous perchlorate and 0.8mol / L perchloric acid at the same time The mixed solution was reacted at 85°C for 4 hours. The reaction is stopped when the detection potential drops to 0.25V.
[0130] 4) Lead sulfate obtained after centrifugal separation of the reaction liquid of the process (3), and a mother liquor containing ferrous perchlorate, ferric perch...
Embodiment 3
[0136] Take 2 kilograms of lead-containing waste from the lead-acid battery production workshop of a company in Hebei and pulverize it into powder by a ball mill. It is determined that it is mainly 95% lead oxide (PbO), 3% lead and a small amount of clay. The process of regenerating lead is as follows:
[0137] 1) After ball milling the above-mentioned lead-containing waste powder in an air atmosphere for 3 hours, sieving with a 60-mesh screen to obtain fine powder, then adding 20 L of 29% NaOH solution, and performing leaching reaction at 100°C. In this process, the lead oxide in the waste and a small amount of lead oxidation newly formed lead oxide and NaOH undergo a complex reaction to form Na 2 [Pb(OH) 4 ]. Measured by EDTA chemical titration, Na 2 [Pb(OH) 4 ] Part of the lead content is 99g / L, and about 0.05 kg of clay-like precipitate remains after filtration.
[0138] 2) The lead-containing mother liquor obtained in the process (1) is purified and then enters an electrolyti...
PUM
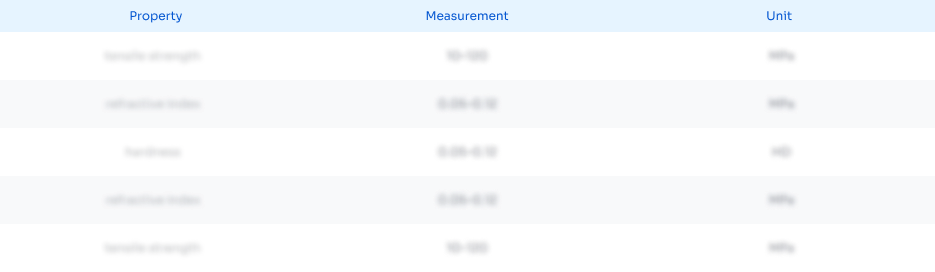
Abstract
Description
Claims
Application Information

- R&D
- Intellectual Property
- Life Sciences
- Materials
- Tech Scout
- Unparalleled Data Quality
- Higher Quality Content
- 60% Fewer Hallucinations
Browse by: Latest US Patents, China's latest patents, Technical Efficacy Thesaurus, Application Domain, Technology Topic, Popular Technical Reports.
© 2025 PatSnap. All rights reserved.Legal|Privacy policy|Modern Slavery Act Transparency Statement|Sitemap|About US| Contact US: help@patsnap.com