Production method of a coating layer for a piece of turbomachinery component, the component itself and the corresponding piece of machinery
A technology for turbines and turbine impellers, applied in coatings, mechanical equipment, machines/engines, etc., can solve problems such as limiting manufacturing costs, and achieve the effect of reducing weight, uniform thickness, and improving productivity
- Summary
- Abstract
- Description
- Claims
- Application Information
AI Technical Summary
Problems solved by technology
Method used
Image
Examples
Embodiment Construction
[0057] In the drawings, (wherein the same numerals correspond to the same parts), as indicated by the present invention (see figure 1 ), the coating 1 is applied by electroless nickel plating on the treated surface 3S of the centrifugal impeller 3, which is made of a light alloy.
[0058] The impellers can be of various types such as centripetal, mixed flow or others. figure 2 Represents a partial cross-section of the centrifugal impeller 3 of a centrifugal compressor, not drawn to scale. The surface of the impeller 3 is coated with the above-mentioned coating 1 according to the present invention and mounted on the shaft 5; please note that the surface 3S of the impeller 3 includes both The outer surface also includes the inner surface (inner channel), but does not include the hole 3F for mounting on the shaft 5 . In particular, the impeller 3 in the figure is a three-dimensional closed impeller. Obviously, the impeller can be of any other type, for example, an open three-d...
PUM
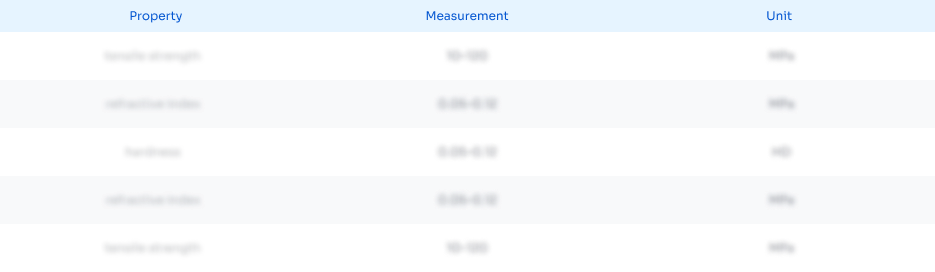
Abstract
Description
Claims
Application Information

- R&D
- Intellectual Property
- Life Sciences
- Materials
- Tech Scout
- Unparalleled Data Quality
- Higher Quality Content
- 60% Fewer Hallucinations
Browse by: Latest US Patents, China's latest patents, Technical Efficacy Thesaurus, Application Domain, Technology Topic, Popular Technical Reports.
© 2025 PatSnap. All rights reserved.Legal|Privacy policy|Modern Slavery Act Transparency Statement|Sitemap|About US| Contact US: help@patsnap.com