Plant fiber starch fully-biodegradable material and preparation method thereof
A technology of biodegradable materials and plant fiber starch, applied in the field of packaging materials, can solve the problems of decreased stability, poor water resistance, refractory, etc., and achieve the effect of improving heat resistance, improving mechanical properties, and low price
- Summary
- Abstract
- Description
- Claims
- Application Information
AI Technical Summary
Problems solved by technology
Method used
Examples
Embodiment 1
[0017] (1) Mix 18 kilograms of corn starch with 0.5 kilograms of plasticizer glycerin and 0.7 kilograms of water, and extrude them through a single screw extruder to obtain 19.2 kilograms of thermoplastic starch, ready for use;
[0018] (2) The coniferous wood is pulverized in a plant crusher, and after screening, 4.5 kg of 50-60 mesh fiber is taken and soaked in 25 kg of chlorinated with a concentration of 8%-12% at a temperature of 30℃~35℃ Lithium / dimethylacetamide solution for 10~30 minutes; then placed in a constant temperature drying oven at 50℃~70℃ for 36h~48h to dry;
[0019] (3) Mix 19.2 kg of thermoplastic starch, processed softwood fiber, 1.2 kg of heat stabilizer polylactic acid, 0.5 kg of dioctyl maleate as a solubilizer, and stir in a high-speed mixer for 8-10 minutes, and then add inorganic fillers 0.5 kg of calcium carbonate and 0.6 kg of cross-linking agent calcium hydroxide, in a high-speed mixer for 10-15 minutes. Finally, extrude and granulate in a twin-screw ex...
Embodiment 2
[0022] (1) Mix 25 kilograms of corn starch with 1 kilogram of plasticizer glycerin and 1.5 kilograms of water, and extrude it through a single screw extruder to obtain 27.5 kilograms of thermoplastic starch, ready for use;
[0023] (2) The coniferous wood is crushed in a plant crusher, after screening, take 10 kg of 50-60 mesh fiber, soak it in 33 kg of chlorinated with a concentration of 8%-12% at a temperature of 30℃~35℃ Lithium / dimethylacetamide solution for 10~30 minutes; then placed in a constant temperature drying oven at 50℃~70℃ for 36h~48h to dry;
[0024] (3) Mix 27.5 kg of thermoplastic starch, processed softwood fiber, 3.5 kg of heat stabilizer polylactic acid, 1.8 kg of dioctyl maleate as a solubilizer, and stir in a high-speed mixer for 8-10 minutes, and then add inorganic fillers 1.2 kg of calcium carbonate and 1 kg of cross-linking agent calcium hydroxide, in a high-speed mixer for 10-15 minutes. Finally, extrude and granulate in a twin-screw extruder with a die tem...
Embodiment 3
[0027] (1) Mix 40 kilograms of corn starch with 1.2 kilograms of plasticizer glycerin and 3 kilograms of water, and extrude 44.2 kilograms of thermoplastic starch through a single-screw extruder, ready for use;
[0028] (2) The coniferous wood is crushed in a plant crusher, and after screening, 20 kg of fibers of 50-60 mesh are taken and immersed in 50 kg of chlorinated fibers with a concentration of 8% to 12% at a temperature of 30°C to 35°C. Lithium / dimethylacetamide solution for 10~30 minutes; then placed in a constant temperature drying oven at 50℃~70℃ for 36h~48h to dry;
[0029] (3) Mix 42 kilograms of thermoplastic starch, processed softwood fiber, 8 kilograms of polylactic acid as a heat stabilizer, 2 kilograms of dioctyl maleate as a solubilizer, and stir in a high-speed mixer for 8-10 minutes, and then add inorganic fillers 1 kg of calcium carbonate and 1 kg of crosslinking agent calcium hydroxide, in a high-speed mixer for 10-15 minutes. Finally, extrude and granulate i...
PUM
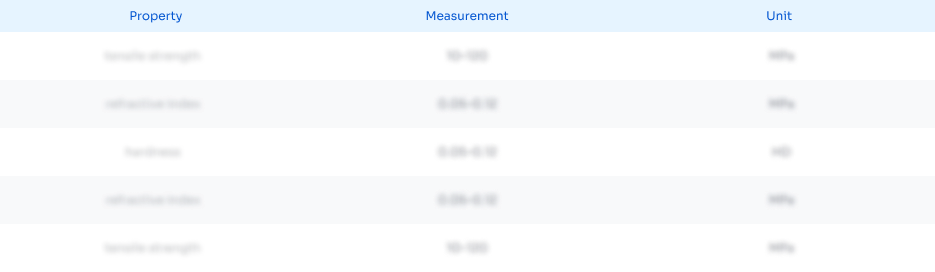
Abstract
Description
Claims
Application Information

- Generate Ideas
- Intellectual Property
- Life Sciences
- Materials
- Tech Scout
- Unparalleled Data Quality
- Higher Quality Content
- 60% Fewer Hallucinations
Browse by: Latest US Patents, China's latest patents, Technical Efficacy Thesaurus, Application Domain, Technology Topic, Popular Technical Reports.
© 2025 PatSnap. All rights reserved.Legal|Privacy policy|Modern Slavery Act Transparency Statement|Sitemap|About US| Contact US: help@patsnap.com