Method for making baking-free bricks by using dye waste water coagulated sludge and baking-free bricks
A technology of dye wastewater and unburned bricks, which is applied in solid waste management, sustainable waste treatment, climate sustainability, etc., can solve the problems of difficulty in flue gas purification, lack of mature and reliable building materials, etc., and achieve resource reduction Reduce costs, improve economic benefits, and consume a large amount of effect
- Summary
- Abstract
- Description
- Claims
- Application Information
AI Technical Summary
Problems solved by technology
Method used
Image
Examples
Embodiment 1
[0040] Select 2000g of dye wastewater, add 16g of lime to neutralize to pH=4~5, then add 6g of polyferric sulfate, and obtain dye wastewater with a water content of 60% (weight percentage) through operations such as coagulation, precipitation, concentration, and pressure filtration Coagulated sludge, in which the organic matter content is 7.5%, the total amount of sulfate is 27.99%, mainly gypsum, and other sulfates, such as sodium sulfate, magnesium sulfate, iron sulfate, aluminum sulfate of different crystal water, the content is very small, these substances It will not have a great impact on the hydration of cement and the durability of concrete products. Its main dry-based chemical components are shown in Table 1.
[0041] Table 1 The main dry basis chemical components in the dye wastewater coagulation sludge of Example 1
[0042] Element
[0043] Weigh 1000g of the above-mentioned dye coagulation sludge with a water content of 60% and add it to the cement mortar...
Embodiment 2
[0045] According to the preparation method similar to Example 1, select 1000g of dye wastewater, add 10g of calcium carbide slag to neutralize to pH=7~8, then add 4g of polyferric sulfate, and prepare the water content through coagulation, precipitation, concentration, pressure filtration and other operations. It is 50% (weight percent) dye wastewater coagulation sludge, organic matter content is 10.5%, total sulfate is 23.99%, and its main dry basis chemical composition is shown in Table 2.
[0046] Table 2 The main dry basis chemical components in the dye wastewater coagulation sludge of Example 2
[0047] Element
[0048] Take by weighing 800g of the above-mentioned dye coagulation sludge with a water content of 50%, join in the cement mortar mixer, add toner 5g, add 650g of sulfate-resistant characteristic cement (the ratio of dye wastewater coagulation sludge to cement weight 1 : 0.8), after stirring evenly, pour into the mold and vibrate, let it stand in the ai...
Embodiment 3
[0050] According to the similar preparation method of Example 1, the dye wastewater coagulation sludge with a water content of 40% (percentage by weight) is prepared, wherein calcium carbide slag is added to adjust to pH=10~11, the organic matter content is 6.5%, and the total amount of sulfate is 33.33%, and its main dry basis chemical composition is shown in Table 3.
[0051] Table 3 The main dry basis chemical components in the dye wastewater coagulation sludge of Example 3
[0052] Element
[0053] Take by weighing 700g of the above-mentioned dye coagulation sludge with a water content of 40%, add 100g of water, join in the cement mortar mixer, add toner 10g, add 700g of special Portland cement (dye wastewater coagulation sewage) without gypsum The weight ratio of mud to cement is 1:1), after stirring evenly, pour it into the model and vibrate it, and let it stand in the air for 24 hours to release the mold; it is cured in water at room temperature for 5 days, an...
PUM
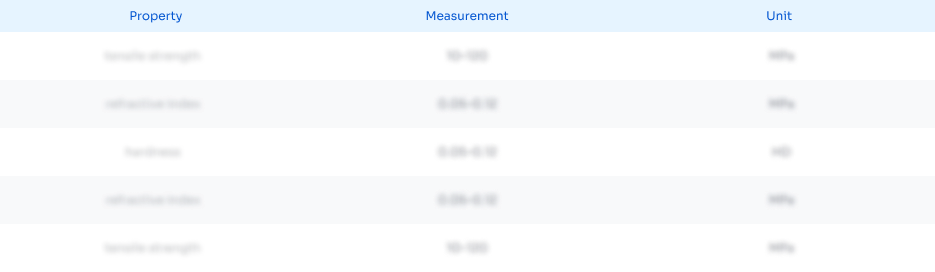
Abstract
Description
Claims
Application Information

- R&D Engineer
- R&D Manager
- IP Professional
- Industry Leading Data Capabilities
- Powerful AI technology
- Patent DNA Extraction
Browse by: Latest US Patents, China's latest patents, Technical Efficacy Thesaurus, Application Domain, Technology Topic, Popular Technical Reports.
© 2024 PatSnap. All rights reserved.Legal|Privacy policy|Modern Slavery Act Transparency Statement|Sitemap|About US| Contact US: help@patsnap.com