Method for extracting nickel and cobalt by processing poor nickel laterite
A nickel laterite and nickel-cobalt technology, applied in the direction of improving process efficiency, can solve the problems of low leaching rate of sulfuric acid leaching at atmospheric pressure, high environmental protection pressure, and magnesium can not be opened, so as to fully utilize heat energy, save energy consumption, The effect of improving equipment productivity
- Summary
- Abstract
- Description
- Claims
- Application Information
AI Technical Summary
Problems solved by technology
Method used
Image
Examples
Embodiment 1
[0039] Prepare materials according to the amount of ore powder: sodium chloride: bituminous coal at 100:6:6. Put mineral powder into the larger heater and heat to 900°C; mix bituminous coal and sodium chloride, and heat the mixture to 800°C in the smaller heater; directly add the above two sets of hot materials into the heat preservation (nearly adiabatic) reactor The internal reaction is 60min., and the reaction temperature is kept above 850°C. If necessary, an appropriate amount of industrial oxygen is added to maintain the temperature. After the above pre-reduction treatment, the metallization rates of nickel-cobalt and iron are 91.3% and 15.4%, respectively.
[0040] After quenching the hot calcine with water, the nickel and cobalt in the calcine are leached while it is still hot. Adopt three-stage downstream leaching operation, the liquid-solid ratio is 3:1; the residence time of materials in each stage is 20 minutes; the temperature of the first, second, and third stage...
Embodiment 2
[0043] Prepare materials according to the ratio of ore powder: calcium chloride: bituminous coal at 100:15:10. Put mineral powder into the larger heater and heat it up to 1100°C; mix bituminous coal with calcium chloride, and heat the mixture into the smaller heater to 500°C; put the above two sets of burning materials directly into the heat preservation (nearly adiabatic) reactor The internal reaction is 30 minutes, and the reaction temperature is kept above 950 ° C. If necessary, an appropriate amount of industrial oxygen is added to maintain the temperature. After the above pre-reduction treatment, the metallization rates of nickel-cobalt and iron are 93.4% and 17.1%, respectively.
[0044]After quenching the hot calcine with water, the nickel and cobalt in the calcine are leached while it is still hot. Adopt three-stage downstream leaching operation, the liquid-solid ratio is 5:1; the residence time of each stage material is 10min; 50~70℃; preheated industrial pure oxyge...
PUM
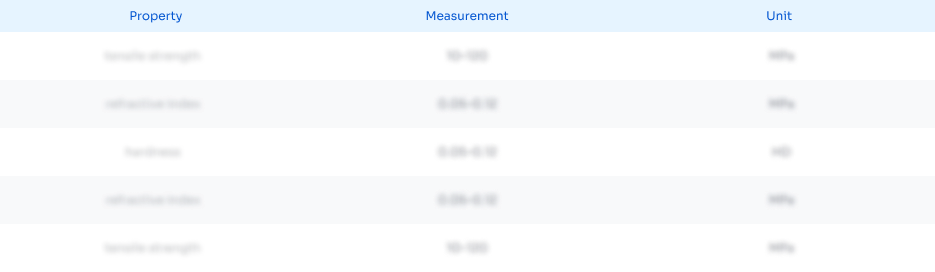
Abstract
Description
Claims
Application Information

- R&D Engineer
- R&D Manager
- IP Professional
- Industry Leading Data Capabilities
- Powerful AI technology
- Patent DNA Extraction
Browse by: Latest US Patents, China's latest patents, Technical Efficacy Thesaurus, Application Domain, Technology Topic, Popular Technical Reports.
© 2024 PatSnap. All rights reserved.Legal|Privacy policy|Modern Slavery Act Transparency Statement|Sitemap|About US| Contact US: help@patsnap.com