Method for improving alumina silica ratio of low-grade bauxite
A low-grade bauxite and aluminum-silicon ratio technology, which is applied in the field of improving the aluminum-silicon ratio of low-grade bauxite and purifying low-grade bauxite, can solve the problems of high cost, long process, and large output of red mud , to achieve the effect of reducing taste requirements and reducing emissions
- Summary
- Abstract
- Description
- Claims
- Application Information
AI Technical Summary
Problems solved by technology
Method used
Image
Examples
Embodiment 1
[0041] (1) After crushing the low-grade bauxite, mix it with solid sodium carbonate at a ratio of 1:1.2 and grind it into a 100-mesh mixed material.
[0042](2), the mixed material obtained in step (1) was roasted for 50 minutes at a temperature of 150°C to obtain roasted clinker; during roasting, the calcining equipment was connected to the gas output pipe and connected to the carbon separation tank.
[0043] (3) Add an appropriate amount of water to the roasted clinker obtained in step (2), and make the solid-to-liquid mass ratio 1:5, and leaching for 40 minutes at a temperature of 50°C. After leaching, filter to obtain filtrate and filter residue respectively. It has been determined that the aluminum-silicon ratio (A / S) in the filter residue is 11, which satisfies the aluminum-silicon ratio condition of the material required for the subsequent Bayer process to produce alumina.
[0044] (4), after the filtrate obtained in step (3) is concentrated to 30% of the original solu...
Embodiment 2
[0047] (1) After the low-grade bauxite is crushed, it is mixed with solid sodium carbonate at a ratio of 1:1 and ground into a 200-mesh mixed material
[0048] (2), the mixed material obtained in step (1) was roasted for 40 minutes at a temperature of 350° C. to obtain roasted clinker; during roasting, the calcining equipment was connected to the gas output pipe and connected to the carbon separation tank.
[0049] (3) Add an appropriate amount of water to the roasted clinker obtained in step (2), and make the solid-liquid mass ratio 1:7, and leaching for 50 minutes under the temperature condition of 40°C. After leaching, filter to obtain filtrate and filter residue respectively.
[0050] (4), after the filtrate obtained in step (3) is concentrated to 20% of the original solution, the CO output from step (2) is fed under normal pressure. 2 Carry out carbonation. The carbon content temperature is 50°C, and the carbon content is stopped when the pH value of the filtrate reache...
Embodiment 3
[0054] (1) After the bauxite tailings are crushed, they are mixed with solid sodium carbonate at a ratio of 1:2 and ground into a 200-mesh mixed material.
[0055] (2), the mixed material obtained in step (1) was roasted for 40 minutes under the temperature condition of 300° C. to obtain roasted clinker; during roasting, the calcining equipment was connected to the gas output pipe and connected to the carbon separation tank.
[0056] (3) Add an appropriate amount of water to the calcined clinker obtained in step (2), and make the solid-liquid mass ratio 1:6, and leaching for 20 minutes at a temperature of 50°C. After leaching, filter to obtain filtrate and filter residue respectively. It has been determined that the aluminum-silicon ratio (A / S) in the filter residue is 10, which satisfies the aluminum-silicon ratio condition of the material required for the subsequent Bayer process to produce alumina.
[0057] (4), after the filtrate obtained in step (3) is concentrated to 30...
PUM
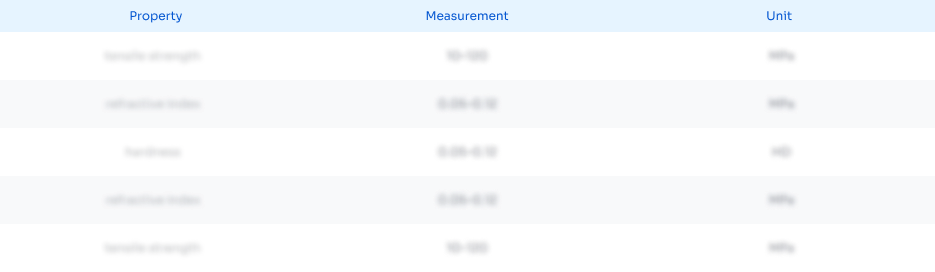
Abstract
Description
Claims
Application Information

- R&D
- Intellectual Property
- Life Sciences
- Materials
- Tech Scout
- Unparalleled Data Quality
- Higher Quality Content
- 60% Fewer Hallucinations
Browse by: Latest US Patents, China's latest patents, Technical Efficacy Thesaurus, Application Domain, Technology Topic, Popular Technical Reports.
© 2025 PatSnap. All rights reserved.Legal|Privacy policy|Modern Slavery Act Transparency Statement|Sitemap|About US| Contact US: help@patsnap.com