Surface hydrophilic modification method for polytetrafluoroethylene bulked membrane
A polytetrafluoroethylene, hydrophilic technology, applied in the field of hydrophilic modification of membrane materials, can solve the problems of cumbersome modification process, complex modification process, short retention time, etc., and achieve the effect of simple treatment process
- Summary
- Abstract
- Description
- Claims
- Application Information
AI Technical Summary
Problems solved by technology
Method used
Image
Examples
Embodiment 1
[0017] (1) Low-voltage glow discharge plasma treatment:
[0018] First, soak the expanded polytetrafluoroethylene membrane in acetone for 5 minutes, then wash it with distilled water for 10 minutes, let it dry naturally, then put the expanded polytetrafluoroethylene membrane into the vacuum chamber 1, and turn on the vacuum pump 2 to pump Vacuum to 5Pa, stabilized for 1 minute, open the pressure reducing valve of the helium cylinder 3, and introduce the reaction gas of He gas to make the pressure reach 15Pa, and after stabilizing for 1 minute, start to use low-temperature plasma to carry out surface treatment on PTFE, the treatment conditions for:
[0019] The plasma reaction gas is He gas, the pressure is 15Pa, the processing power is 100W, and the processing time is 60s;
[0020] (2) Acrylic acid graft modification treatment:
[0021] First, make a solution of acrylic acid, put it in a constant temperature water bath to keep the temperature at 60°C, and then expose the exp...
Embodiment 2
[0023] (1) Low-voltage glow discharge plasma treatment:
[0024] First, soak the expanded polytetrafluoroethylene film to be treated in acetone for 10 minutes, then wash it with distilled water for 20 minutes, let it dry naturally, then put the expanded polytetrafluoroethylene film into the vacuum chamber 1, and turn on the vacuum pump 2 to pump Vacuum to 3Pa, after 2 minutes of stabilization, open the pressure reducing valve of the helium cylinder 3, and let in the reaction gas of He gas to make the pressure reach 30Pa, and after 2 minutes of stabilization, start to use low-temperature plasma to carry out surface treatment on PTFE, the treatment conditions for:
[0025] The plasma reaction gas is He gas, the pressure is 30Pa, the processing power is 50W, and the processing time is 90s;
[0026] (2) Acrylic acid graft modification treatment:
[0027] First, make a solution of acrylic acid, put it in a constant temperature water bath to keep the temperature at 50°C, and then ...
Embodiment 3
[0029] (1) Low-voltage glow discharge plasma treatment:
[0030] First, soak the expanded polytetrafluoroethylene membrane in acetone for 7 minutes, then wash it with distilled water for 15 minutes, let it dry naturally, then put the expanded polytetrafluoroethylene membrane into the vacuum chamber 1, and turn on the vacuum pump 2 to pump Vacuum to 4Pa, stabilize for 3 minutes, open the pressure reducing valve of the helium cylinder 3, and let the reaction gas of He gas to make the pressure reach 50Pa. for:
[0031] The plasma reaction gas is He gas, the pressure is 50Pa, the processing power is 150W, and the processing time is 30s;
[0032] (2) Acrylic acid graft modification treatment:
[0033] First, make a good solution of acrylic acid, put it in a constant temperature water bath to keep the temperature at 70°C, and then expose the expanded polytetrafluoroethylene film treated in step (1) to the air for 20 minutes, then immerse it in the prepared acrylic acid In the sol...
PUM
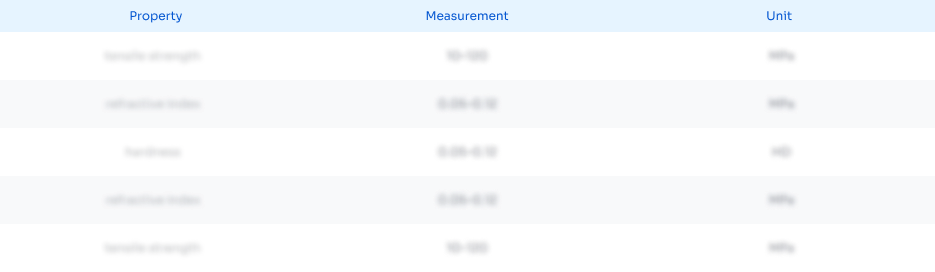
Abstract
Description
Claims
Application Information

- Generate Ideas
- Intellectual Property
- Life Sciences
- Materials
- Tech Scout
- Unparalleled Data Quality
- Higher Quality Content
- 60% Fewer Hallucinations
Browse by: Latest US Patents, China's latest patents, Technical Efficacy Thesaurus, Application Domain, Technology Topic, Popular Technical Reports.
© 2025 PatSnap. All rights reserved.Legal|Privacy policy|Modern Slavery Act Transparency Statement|Sitemap|About US| Contact US: help@patsnap.com