Polyalcohol modified epoxy resin carbon fiber emulsion sizing agent component and preparation method thereof
An epoxy resin emulsion, epoxy resin technology, applied in carbon fiber, fiber processing, textiles and papermaking, etc., can solve problems such as broken filaments, fluff, etc., and achieve less filaments, uniform particle size distribution, pH value stability and excellent high temperature stability
- Summary
- Abstract
- Description
- Claims
- Application Information
AI Technical Summary
Problems solved by technology
Method used
Image
Examples
Embodiment 1
[0016] Take polyethylene glycol 1000 as modifier, hydrochloric acid as initiator, and epoxy resin as bisphenol A type epoxy resin. According to the mol ratio of polyethylene glycol and bisphenol A type epoxy resin 1.5: 1, take the raw material, and take the hydrochloric acid quality according to 0.1% of the sum of polyethylene glycol and bisphenol A type epoxy resin quality, then The above-mentioned three kinds of raw materials were mixed, placed in an environment of 60° C., and heated and stirred for 2 hours to obtain a modified epoxy resin. The following reactions occur during mixing:
[0017]
[0018] Add ammonia water dropwise to the above-mentioned modified epoxy resin solution to make the pH of the solution neutral, continue heating and stirring at 60°C for 1 hour, and add deionized water to the above-mentioned neutral solution at a temperature of 70°C, stir and Uniform dispersion makes the solution self-emulsified to obtain a modified epoxy resin emulsion.
[0019]...
Embodiment 2
[0030] Mix polyethylene glycol 1000, bisphenol A epoxy resin, epoxy diluent and initiator ammonium persulfate, place the mixture under 95°C environment, heat and stir for 2 hours; Add deionized water into the neutral solution, stir and disperse evenly to make the solution self-emulsified, and prepare the modified epoxy resin emulsion. Wherein the molar ratio of polyethylene glycol 1000 to bisphenol A epoxy resin is 1:1, and the mass of initiator ammonium persulfate added is 1% of the sum of the mass of polyethylene glycol 1000 and bisphenol A epoxy resin.
[0031] 1. The stable range of PH value of modified epoxy resin emulsion: 1-14;
[0032] 2. High-temperature stability of modified epoxy resin emulsion: keep it in an oven at 70°C for 20 days without breaking the emulsion.
[0033] 3. Solid content: the solid content of sizing agent components can be controlled and formulated;
[0034] 4 wool silk amount: the experimental results are shown in Table 2:
[0035] Table 2 The...
Embodiment 3
[0039] Mix polyethylene glycol 1000, bisphenol A epoxy resin, epoxy diluent and initiator potassium persulfate, place the mixture under 120°C environment, heat and stir for 2 hours; Add deionized water into the neutral solution, stir and disperse evenly to make the solution self-emulsified, and prepare the modified epoxy resin emulsion. . Wherein the molar ratio of polyethylene glycol 1000 to bisphenol A epoxy resin is 1:1.5, and the mass of initiator potassium persulfate added is 1% of the sum of the mass of polyethylene glycol 1000 and epoxy resin.
[0040] 1. The stable range of PH value of modified epoxy resin emulsion: 1-14;
[0041] 2. High-temperature stability of modified epoxy resin emulsion: keep it in an oven at 70°C for 20 days without breaking the emulsion.
[0042] 3. Solid content: the solid content of sizing agent components can be controlled and formulated;
[0043] 4 wool silk amount: the experimental results are shown in Table 3:
[0044] Table 3 wool si...
PUM
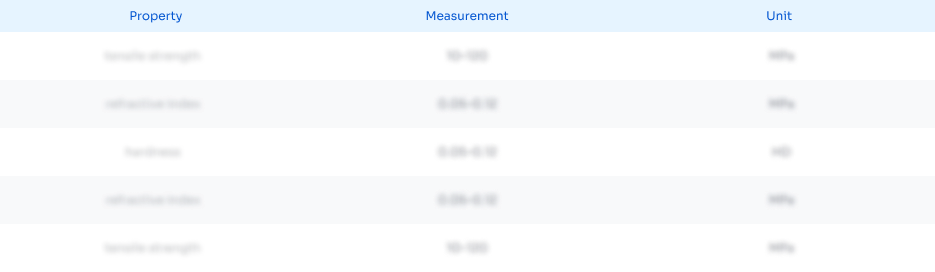
Abstract
Description
Claims
Application Information

- R&D
- Intellectual Property
- Life Sciences
- Materials
- Tech Scout
- Unparalleled Data Quality
- Higher Quality Content
- 60% Fewer Hallucinations
Browse by: Latest US Patents, China's latest patents, Technical Efficacy Thesaurus, Application Domain, Technology Topic, Popular Technical Reports.
© 2025 PatSnap. All rights reserved.Legal|Privacy policy|Modern Slavery Act Transparency Statement|Sitemap|About US| Contact US: help@patsnap.com