Wall surface energy-saving decorative board and manufacturing method thereof
A production method and technology of decorative boards, applied in the manufacture of tools, ceramic products, and other household appliances, can solve the problems of non-compliance with environmental protection principles, consumption of mineral resources, and single decorative style, so as to reduce the consumption of mineral resources and simplify the production process , The effect of low thermal conductivity
- Summary
- Abstract
- Description
- Claims
- Application Information
AI Technical Summary
Problems solved by technology
Method used
Examples
Embodiment 1
[0017] A wall energy-saving decorative panel described in the embodiment of the present invention is made of the following raw materials: 10kg of cement, 50kg of fly ash, 20kg of water, 6kg of glass fiber mesh, 3kg of high molecular polymer, and 0.1-kg of foaming agent. 0.5, air-entraining agent 0.01-0.1, foam stabilizer 0.01-0.5, auxiliary material 10kg; the auxiliary material can be bamboo chips, high molecular polymer is epoxy, acrylic acid or polyvinyl acetate, and foaming agent can be surfactant Or 12 alkyl sodium sulfates, the foam stabilizer can be alkyl alcohol amide, fatty alcohol polyoxyethylene ether or sodium sulfate.
[0018] A method for making a wall energy-saving decorative panel described in an embodiment of the present invention includes the following steps:
[0019] 1) Mixing: Mix 10kg cement, 50kg fly ash and 10kg water, then add 3kg polyvinyl acetate and mix well;
[0020] 2) Make slurry: put the uniformly mixed raw materials in step 1) in the mixer, then...
Embodiment 2
[0026] A wall energy-saving decorative panel described in the embodiment of the present invention is made of the following raw materials: 20kg of cement, 55kg of fly ash, 20kg of water, 6kg of glass fiber mesh, 5kg of high molecular polymer, and 0.1-kg of foaming agent. 0.5, air-entraining agent 0.01-0.1, foam stabilizer 0.01-0.5, auxiliary material 6kg; the auxiliary material can be bamboo chips, wood chips, rattan or hemp, high molecular polymer is epoxy acrylic acid or polyvinyl acetate, foaming agent It can be surfactant or 12-alkyl sodium sulfate, and the foam stabilizer can be alkyl alcohol amide, fatty alcohol polyoxyethylene ether or sodium sulfate.
[0027] The steps of the manufacturing method of an energy-saving decorative panel for walls described in the embodiment of the present invention are the same as those in Embodiment 1.
Embodiment 3
[0029] A wall energy-saving decorative panel described in the embodiment of the present invention is made of the following raw materials: 15 kg of cement, 52.5 kg of fly ash, 20 kg of water, 6 kg of glass fiber mesh, 4 kg of polyvinyl acetate, and 0.1 kg of foaming agent. -0.5kg, air-entraining agent 0.01-0.1kg, foam stabilizer 0.01-0.5kg, auxiliary material 12kg; the auxiliary material can be bamboo chips, wood chips, rattan or hemp, and the foaming agent can be surfactant or 12 alkyl sulfuric acid Sodium, the foam stabilizer can be alkanolamide, fatty alcohol polyoxyethylene ether or sodium sulfate.
[0030] The steps of the manufacturing method of an energy-saving decorative panel for walls described in the embodiment of the present invention are the same as those in Embodiment 1.
[0031] The method of the present invention consumes less energy in the production process, only some electric energy is needed for pulping and autoclaving, and the whole process does not need to...
PUM
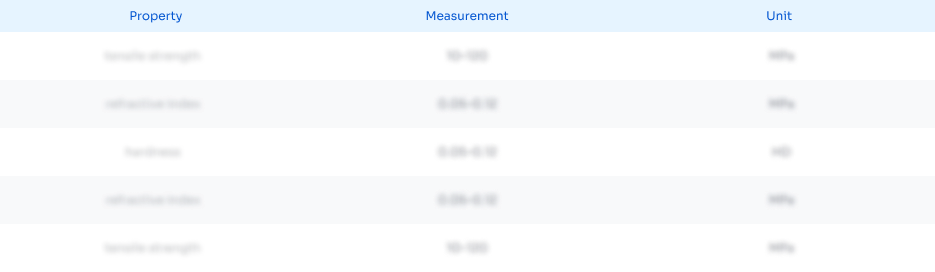
Abstract
Description
Claims
Application Information

- R&D
- Intellectual Property
- Life Sciences
- Materials
- Tech Scout
- Unparalleled Data Quality
- Higher Quality Content
- 60% Fewer Hallucinations
Browse by: Latest US Patents, China's latest patents, Technical Efficacy Thesaurus, Application Domain, Technology Topic, Popular Technical Reports.
© 2025 PatSnap. All rights reserved.Legal|Privacy policy|Modern Slavery Act Transparency Statement|Sitemap|About US| Contact US: help@patsnap.com