Production method for spherical active carbon
A technology of spherical activated carbon and production method, which is applied in the direction of chemical instruments and methods, inorganic chemistry, non-metallic elements, etc., can solve the problems of large spherical activated carbon, low specific surface area, high mechanical strength, etc., and achieve high reliability, simple preparation process, The effect of cheap raw materials
- Summary
- Abstract
- Description
- Claims
- Application Information
AI Technical Summary
Problems solved by technology
Method used
Image
Examples
Embodiment 1
[0020] The production method of spherical activated carbon of the present invention may further comprise the steps:
[0021] (1) Mix 100g of glucose, 1g of rhamnolipid, 5g of cetyltrimethylammonium bromide, 10g of humic acid and 1000g, and ultrasonically react at 30°C for 0.5h to dissolve the glucose and mix all the raw materials uniform. Then transfer to the hydrothermal synthesis kettle, conduct hydrothermal reaction at 160°C for 18 hours, filter after the reaction is completed, wash the precipitated product, and obtain hydrothermal carbon spheres;
[0022] (2) The hydrothermal charcoal spheres prepared in step (1) were raised to 500°C at a heating rate of 12°C / min under the protection of nitrogen, kept for 15 hours, and cooled to room temperature naturally to obtain carbonized charcoal spheres;
[0023] (3) Mix the carbonized carbon spheres obtained in step (2) with sodium hydroxide in a mass ratio of 1:2, and raise the temperature to 850° C. at a rate of 5° C. / min under n...
Embodiment 2
[0025] The production method of spherical activated carbon of the present invention may further comprise the steps:
[0026] (1) Mix 110g of glucose, 1g of rhamnolipid, 4g of cetyltrimethylammonium bromide, 11g of humic acid and 1000g, and ultrasonically react at 28°C for 1 hour to dissolve the glucose and mix all the raw materials evenly . Then transfer to a hydrothermal synthesis kettle, conduct a hydrothermal reaction at 180°C for 18 hours, filter after the reaction is completed, wash the precipitated product, and obtain hydrothermal carbon spheres;
[0027] (2) The hydrothermal carbon spheres prepared in step (1) were raised to 550° C. at a heating rate of 10° C. / min under nitrogen protection, kept for 8 hours, and naturally cooled to room temperature to obtain carbonized carbon spheres;
[0028] (3) Mix the carbonized carbon spheres obtained in step (2) with sodium hydroxide in a mass ratio of 1:3, raise the temperature to 800° C. at a rate of 8° C. / min under nitrogen pr...
Embodiment 3
[0030] The production method of spherical activated carbon of the present invention may further comprise the steps:
[0031] (1) Mix 120g of glucose, 1g of rhamnolipid, 5g of cetyltrimethylammonium bromide, 12g of humic acid and 1000g, and ultrasonically react at 25°C for 1 hour to dissolve the glucose and mix all the raw materials evenly . Then transfer to a hydrothermal synthesis kettle, conduct a hydrothermal reaction at 200°C for 20 hours, filter after the reaction is completed, wash the precipitated product, and obtain hydrothermal carbon spheres;
[0032] (2) The hydrothermal charcoal spheres prepared in step (1) were raised to 600°C at a heating rate of 10°C / min under the protection of nitrogen, kept for 6 hours, and cooled to room temperature naturally to obtain carbonized charcoal spheres;
[0033] (3) Mix the carbonized carbon spheres obtained in step (2) with sodium hydroxide at a mass ratio of 1:5, and raise the temperature to 900°C at a rate of 10°C / min under nit...
PUM
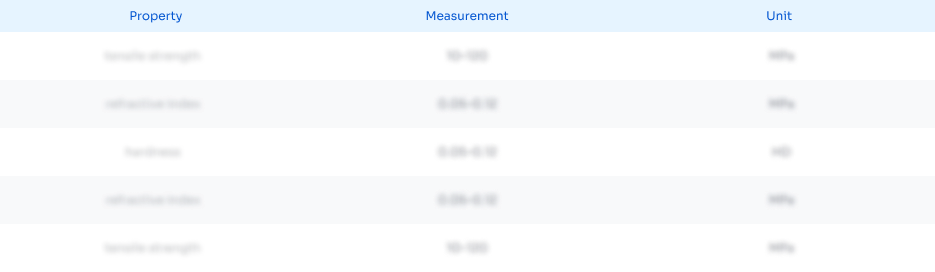
Abstract
Description
Claims
Application Information

- Generate Ideas
- Intellectual Property
- Life Sciences
- Materials
- Tech Scout
- Unparalleled Data Quality
- Higher Quality Content
- 60% Fewer Hallucinations
Browse by: Latest US Patents, China's latest patents, Technical Efficacy Thesaurus, Application Domain, Technology Topic, Popular Technical Reports.
© 2025 PatSnap. All rights reserved.Legal|Privacy policy|Modern Slavery Act Transparency Statement|Sitemap|About US| Contact US: help@patsnap.com