Halogen-free and phosphorous-free flame-retardant synthetic resin adhesive used for flexible copper clad laminate
A technology for synthesizing resins and adhesives, applied in the direction of online phenolic epoxy resin adhesives, adhesives, epoxy resin glue, etc., which can solve the problems that no halogen-free phosphorus-free flame-retardant epoxy resin composition has been reported.
- Summary
- Abstract
- Description
- Claims
- Application Information
AI Technical Summary
Problems solved by technology
Method used
Image
Examples
Embodiment 1
[0039] 30 parts of biphenyl epoxy resin (NC-3000H), 45 parts of elastomer modified epoxy resin (Epon58005), 10 parts of polyester resin (Vylon30P), 20 parts of synthetic rubber (Nipol 1072), melamine cyanurate 35 parts, 20 parts of aluminum hydroxide and 100 parts of methyl ethyl ketone are placed in a ball mill to fully grind, then add 10 parts of diaminodiphenyl sulfone, 1.0 parts of 2-ethyl 4-methylimidazole and 390 parts of methyl ethyl ketone, and continue stirring at high speed After 12 hours, adjust the solid content of the glue solution to 35±2wt%, and mix it into a halogen-free and phosphorus-free epoxy resin adhesive.
[0040]The adhesive is coated on a polyimide insulating film with a thickness of 25 μm by a coating machine, and the thickness of the coating is 20±2 μm, and then dried in an oven at 80 ° C for 10 minutes to remove the organic solvent, and 35 μm electrolytic copper foil The hot pressing rollers are combined together, and the composite is cured at 150°C...
Embodiment 2
[0042] The specific formula is shown in Table 1, Example 2, and the preparation method of the adhesive is the same as in Example 1. Apply the prepared adhesive on a polyimide insulating film with a thickness of 12.5 μm by a coating machine, and the thickness of the coating is 20 μm, and then dry it through a 100 ° C oven for 5 minutes to remove the organic solvent, and 35 μm electrolytic copper foil After being combined by hot pressing rollers, the composite was cured at 150°C for 2 hours and at 170°C for 2 hours to obtain a flexible copper-clad laminate, and its properties are shown in Table 2.
Embodiment 3
[0044] The specific formula is shown in Table 1, Example 3, and the preparation method of the adhesive is the same as in Example 1. The prepared adhesive is coated on a polyimide insulating film with a thickness of 25 μm by a coating machine. The hot pressing rollers are combined together, and the composite is cured at 150°C for 2 hours and at 170°C for 2 hours to obtain a flexible copper clad laminate, and its properties are shown in Table 2.
PUM
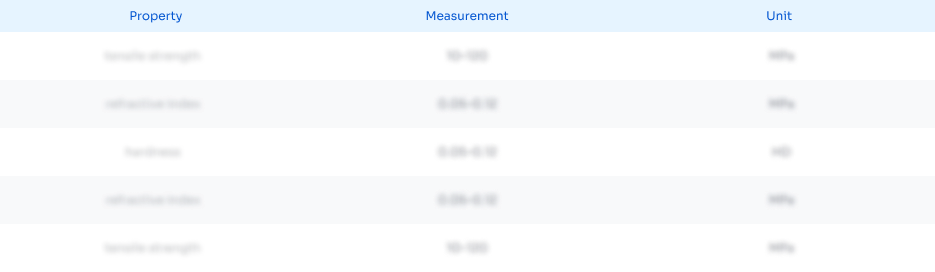
Abstract
Description
Claims
Application Information

- R&D
- Intellectual Property
- Life Sciences
- Materials
- Tech Scout
- Unparalleled Data Quality
- Higher Quality Content
- 60% Fewer Hallucinations
Browse by: Latest US Patents, China's latest patents, Technical Efficacy Thesaurus, Application Domain, Technology Topic, Popular Technical Reports.
© 2025 PatSnap. All rights reserved.Legal|Privacy policy|Modern Slavery Act Transparency Statement|Sitemap|About US| Contact US: help@patsnap.com