Surface-stuck type magnetic element as well as manufacturing method and coil thereof
A surface-mounted, magnetic component technology, applied in the direction of electrical components, magnetic objects, devices using electro-magnetic effects, etc., can solve the problems of different lengths, affecting electrical performance, poor flatness of pins 111, etc.
- Summary
- Abstract
- Description
- Claims
- Application Information
AI Technical Summary
Problems solved by technology
Method used
Image
Examples
Embodiment Construction
[0061] Some typical embodiments embodying the features and advantages of the present invention will be described in detail in the following description. It should be understood that the invention is capable of various changes in different forms, all without departing from the scope of the invention, and that the description and drawings therein are illustrative in nature and not intended to limit the invention.
[0062] see figure 2 and refer to Figure 3A ,in figure 2 is the manufacturing flow chart of the surface mount type magnetic element of the first preferred embodiment of the present invention, and Figure 3A It is a schematic diagram of the manufacturing process of the surface mount magnetic element according to the first preferred embodiment of the present invention. Such as figure 2 As shown, the method for manufacturing the surface mount type magnetic element 2 in this embodiment is to firstly provide the magnetic permeable component 20 and the coil 21 (step...
PUM
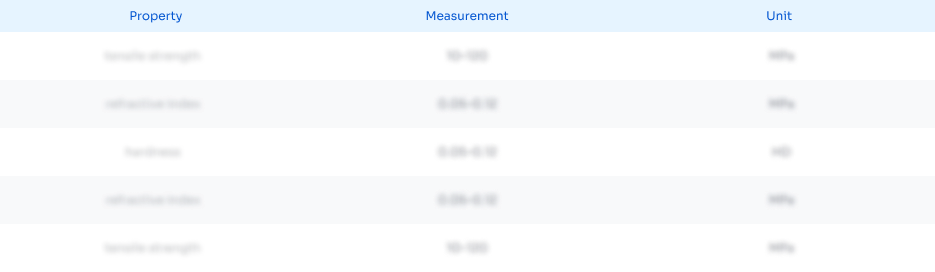
Abstract
Description
Claims
Application Information

- R&D
- Intellectual Property
- Life Sciences
- Materials
- Tech Scout
- Unparalleled Data Quality
- Higher Quality Content
- 60% Fewer Hallucinations
Browse by: Latest US Patents, China's latest patents, Technical Efficacy Thesaurus, Application Domain, Technology Topic, Popular Technical Reports.
© 2025 PatSnap. All rights reserved.Legal|Privacy policy|Modern Slavery Act Transparency Statement|Sitemap|About US| Contact US: help@patsnap.com